Fluorescent Penetrant Testing: Non-Destructive Testing for Critical Components
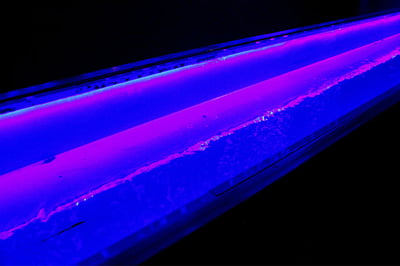
What Does Penetrant Testing Do for Surface Finishing?
For manufacturing components, especially those with critical functions, penetrant testing is the non-destructive test (NDT) method that checks for surface flaws that could result in component instabilities if not found. Used for quality control, regulatory compliance, failure analysis and routine maintenance, components may be tested more than once over their lifetime. Therefore, a testing method that causes no damage, but is in-depth enough to check for the smallest flaws is essential.
As the most precise method of liquid penetrant testing, Fluorescent Penetrant Testing (FPT) is able to penetrate the smallest of cracks, fractures, laps & seams; the fluorescent properties of the dye highlight the imperfections for greater contrast during the inspection stage.
Continue reading to learn about the Fluorescent Penetrant Testing method and the extent of its precision detection.
What are the Fluorescent Penetrants?
The fluorescent dyes that make this precision detection possible require a low surface tension (also known as the sensitivity level) to penetrate the minute imperfections.
Available from low to high sensitivity, the dye used is determined by the nature of the component. For a component that has a rougher surface, such as the raw finish of an additive manufactured (3D printed) part, a lower sensitivity penetrant would be used so it doesn’t highlight the background profile of the component’s surface. On the other hand, precision machined components like turbine blades with smoother surfaces would reveal smaller imperfections, requiring a higher sensitivity dye.
Appling Penetrant for NDT Testing
Before the application can begin, the components must be pre-cleaned to remove any contaminates that could contribute to false indications. The penetrant can be applied once cleaned and dried using methods such as solvent cleaning, vapour rinsing and media blasting.
The penetrant can be applied by dipping, spraying, or brushing and requires time to sit and soak into any imperfections on the surface; this dwell time varies from 5 to 30 minutes.
When set, the excess penetrant needs to be removed by another cleaning method not as thorough as the pre-treatment but enough to remove all the dye not located in potential flaws. The most common removal process includes water washers, solvents & emulsifiers; one or two options would be used depending on the penetrant. If the penetrant is highly sensitive, it is probably oil-based, so an emulsifier would have to be used first to be cleaned by an aqueous spray.
In the last stage before inspection, a developer chemical needs to be applied to draw out the penetrant and form the bleed-out, the remaining dye residue indicating any flaws & imperfections. The developer requires 10-30 minutes for this blotting action to occur for inspection.
Ready for inspection, the components are taken to a dark room/area lit with ultraviolet radiation (UV-A) to react with the fluorescent dye; a yellow/green glow highlights any flaws to the component surface.
Uses for Fluorescent Penetrant Testing
Fundamental in industries such as aerospace, automotive and power generation, it is in these industries that a lot of critical components are manufactured. From turbine blades to large structural castings, these parts have no room for error once installed, so making sure they meet quality control is vital.
Components tested with FPT can be made of metal, plastic, ceramics and composites. These materials all undergo physical and chemical processes during manufacturing that can all cause damage which could cause component failure. Processes like forging, quenching, grinding and surface finishing all come with stress risks to the component.
Why Should You Use Fluorescent Penetrant Testing?
Fast, easy and efficient, Fluorescent Penetrant Testing is the method for testing components repeatedly, providing clear results without wear to the parts. Able to detect the smallest flaws in simple to complex components of various materials in large quantities and short inspection times.
Machines & equipment for sale
- Surface Treatment
- Cleaning & Degreasing
- Polishing & Belt Linishing
- Mass Finishing
- Ovens & Furnaces
- Process Cooling
- Shot Blasting
- Dust & Fume Extraction
- Air Compressors
- Rectifiers & Transformers
- Miscellaneous
- Latest Stock
- Special Offers
- Direct From Site Clearances
- Auctions
- Brand New Machines
- Available Immediately
- Sell Your Machine
Machine Alert
Get the latest machines emailed directly to you as they become available to buy online. Sign Up Now