Hydrogen Cell Anode Manufacturing: An Opportunity for the Plating Industry
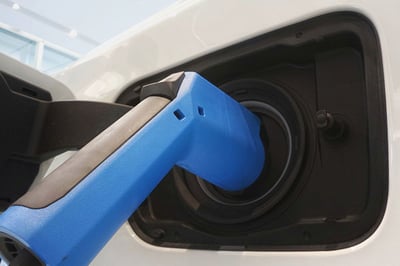
As our energy sources transition to renewable power, the manufacturing technology to support this change is also on the increase. The funding and investment being poured into renewable energy is huge and is driving the rapid commercialisation of technology. This is creating opportunities for existing industries to use their expertise and diversify.
Hydrogen based energy storage and use is one of the oil and gas alternatives that’s set to grow rapidly as demonstrated by JCB’s recent development of Hydrogen Fuel engines. Hydrogen based energy creates energy by combining hydrogen and oxygen with only emission friendly by-products.
Playing a key role in the rise of the hydrogen energy industry, the fuel cells that make up the industry wouldn’t be as advanced and efficient as they are without platinum – and that is where this opportunity is created for the plating industry. Working with high value materials and high quality requirements suits experienced companies and has the potential for strong margins.
How is Platinum Being Used in Hydrogen Fuel Cells?
Hydrogen fuel cells, or more specifically Polymer Electrolyte Membrane (PEM) fuel cells have three main features that make up the cell. Two electrodes and a polymer electrolyte membrane between them. The cell is made up of a negative electrode (called the anode in this case) and a positive electrode (cathode in this case); the anode being the electrode the platinum is involved with, controlling the desired chemical reaction as the catalyst.
The anode first receives a supply of hydrogen that reacts with the platinum coated anode upon contact. This results in the electron and proton particles of the hydrogen being divided.
It’s from here that each of the electrons and protons want to make their way to the other electrode, the cathode, but both can’t travel the same way. The polymer electrolyte membrane that divides the electrodes is a proton conducting, therefore allowing the proton particles to go straight through. While the electrons travel via an external circuit, producing an electrical charge that generates the power from hydrogen fuel cells.
Once the electrons reunite with the protons in the cathode, they join with oxygen to produce water and low levels of heat.
How is Platinum Being Used to Generate Green Hydrogen?
To use Hydrogen you need to generate it. This is achieved in several ways all colour coded based on the production method. for instance, Brown hydrogen is from coal, pink from excess energy in nuclear and green hydrogen from renewable energy. Being able to convert excess energy into Hydrogen is one way of storing energy for times when generation is lower or moving it around the world and onto platforms where battery technology isn't suitable.
Generation of hydrogen can be achieved with electrolysis, splitting water in Hydrogen and Oxygen. The technology to achieve this involves anodes and cathodes in electrolysis cells and members to control the substrates.
Just like fuel cells platinum is the metal of choice for the electrodes so offers the same opportunities for anyone seeking to manufacture components for this industry.
Why Platinum for Hydrogen Fuel Cells?
As a noble metal, the superior properties of platinum are matched by no other metals. Even though there are other metals that could be used for coating the anodes, the surface coating must be platinum as its corrosive resistance in an anodic atmosphere is unparalleled to all other materials.
The structural stability of platinum as a material can withstand complex chemical reactions without wear, yet it also has a high conductivity density to allow particles to pass through it. This durability and flexibility also allow it to conduct electrolytes without producing an insulating film which can interfere with the electrical performance of the fuel cell.
How Can You Manufacture Platinum Coated Anodes and Cathodes?
A process that could require multiple layers, the method starts with the supporting structure of another metal, most typically titanium or niobium. As the base metal is that of a lower resistance, it requires platinum to protect it from the electrolyte within the fuel cell or it will produce an oxide film making it ineffective.
To prepare the supporting structure for application, it is first cleaned the remove any oxide skins masking the surface for a stronger adhesion bond to the platinum. The natural form of platinum is solid so for the platinum-bearing preparation, the material is dissolved into a thermally decomposable compound so it can be applied to the structural component.
When applying a layer, the application process can be repeated as long as the layers are dried between each layer in an oxidising atmosphere at 350 °C to 550°C. The temperature is critical for the drying as too cold would result in a weak adhesion between the metals and too hot would reduce the long-term efficiency of the anode.
The final coating resulting in a platinum thickness of 0.25mm to 0.5mm.
Benefits of PEM Hydrogen Fuel Cells
Able to be classified as Green Hydrogen because the fuel cells produce no emissions, the cells have a much longer shelf life when compared to a standard battery.
Due to factors like the low operating temperature, compact design and no corrosive fluid hazards, PEM fuel cells are already popular in the automotive industry. Hydrogen can be as practical to refuel as a diesel vehicle and can be installed in fuel cell electric vehicles (FCEV) which you may have already seen for yourself on the road.
Although these cells are not just limited to mobile purposes, one fuel cell will only produce a matter of kilowatts but stack them together... it becomes megawatts suitable for storing energy generated by generation technology like wind and solar.
Future of Platinum Plating
Prominent in one of the quickest rising industries, platinum will be essential in the movement towards ‘greener’ energy as efforts continue on a global scale. Offering potential with fewer limitations in comparison to other renewable energies such as solar or wind, it has already proven itself to be adaptable to many of today’s technologies, most noticeable for the automotive industry.
Exclusive to Riley Surface World, we have available an Automatic, Immersion Platinum Plating Line in one of our clearance events. Including a complete pre-treatment/cleaning, application and post-treatment facility, if you want to upgrade your plating line or get into the industry, this is the opportunity for you.
For more information, contact Helen from our Direct From Site team today at 01922 749 284 or [email protected].
Machines & equipment for sale
- Surface Treatment
- Cleaning & Degreasing
- Polishing & Belt Linishing
- Mass Finishing
- Ovens & Furnaces
- Process Cooling
- Shot Blasting
- Dust & Fume Extraction
- Air Compressors
- Rectifiers & Transformers
- Miscellaneous
- Latest Stock
- Special Offers
- Direct From Site Clearances
- Auctions
- Brand New Machines
- Available Immediately
- Sell Your Machine
Machine Alert
Get the latest machines emailed directly to you as they become available to buy online. Sign Up Now