Platinum Plating: The Solution to Having an Everlasting Turbine Blade
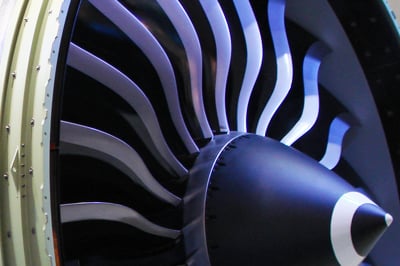
A major maintenance problem for gas turbine engine operators is the degradation of high-pressure turbine blades - this leads to unacceptably high rejection rates of these components in performance engines as a result of severe hot corrosion attacks. Turbine blades in gas turbine engines operate at very high temperatures and in an atmosphere that is highly oxidizing, and can be contaminated with fuel residues and sea water salts.
As the components in turbines are expensive to produce and are exposed to high stresses while operating finding solutions has been critical for safety and quality.
What is Platinum?
Pure platinum is a white metal, very similar in appearance to silver- its occurrence is rare in nature but it can now be found in up to 20% of consumer goods produced around the world. Platinum is one of the most ductile, and dense metals. It is also malleable in which it has the ability to deform without losing its strength. It does not tarnish in air nor dissolve in most harsh acids. Pure platinum has a very high melting point (1768°C, 3214°F). This puts it much higher than gold or silver (both have melting points around 1,000°C). All these platinum characteristics make it an extremely important metal of uses in industrial applications.
How does Platinum help?
A solution to maintain turbine blades is to coat the base metal with platinum, this makes the blade resist both high temperature oxidation and hot corrosion. At the same time it has some degree of erosion resistance and is able to tolerate minor impact damage.
Service life is increased by a factor of three to four times. Platinum deposits in turbine blades are typically 5 μm in thickness and are then put through a pack diffusion process to form a platinum alumina composite deposit.
Platinum also helps in surface smoothness, especially when simple aluminides form grain boundaries, that during the oxidation process are the pathways for oxidation, creating a rumpled surface; platinum keeps the oxidation rate even and does not form the grain boundaries that a simple aluminide does.
How to coat with Platinum?
Platinum plating occurs through electroplating.
Electroplating uses electricity and an electrolyte solution, a bath of chemicals including the metal that needs to be deposited. Once the turbine blade is suspended into the electrolyte a very carefully controlled electric current is passed through the blade and solution to deposit the ions of this metal onto the surface of the turbine blade. This is how coating as thin as 5μm (5 microns is 5 millionths of a meter) can be permanently added to the blade.
To get to the point of electroplating a component (the turbine blade) it must be very clean, sometimes requires preparation using acids or alkalis, electroplating with other "base coat" metals and/or several coats of the finishing metal to gradually build up layers. This is why any electroplating plant has many process stages before the final product is complete.
This type of plating offers many benefits to the turbine blade, such as its ability to create a corrosion-resistance surface, conductivity, hydrogen absorption, resistance to heat and it does not tarnish.
Platinum Plating Line for Sale
Riley Surface World currently has a Platinum Plating Line for sale. It includes pre treatment and post treatment plant and is available for export worldwide.
Additionally Riley Surface World is always keen to hear from anyone with redundant platinum plating plant, or any large surface treatment plant. Often it can be reused elsewhere returning funds to the seller and reducing the considerable waste involved in scrapping plant.
Machines & equipment for sale
- Surface Treatment
- Cleaning & Degreasing
- Polishing & Belt Linishing
- Mass Finishing
- Ovens & Furnaces
- Process Cooling
- Shot Blasting
- Dust & Fume Extraction
- Air Compressors
- Rectifiers & Transformers
- Miscellaneous
- Latest Stock
- Special Offers
- Direct From Site Clearances
- Auctions
- Brand New Machines
- Available Immediately
- Sell Your Machine
Machine Alert
Get the latest machines emailed directly to you as they become available to buy online. Sign Up Now