The Emergence of Architectural Aluminium
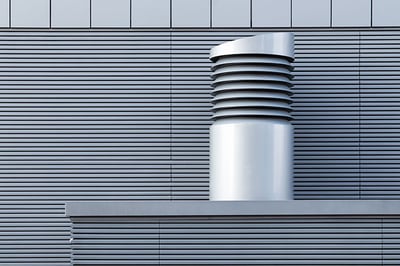
What is Aluminium?
Aluminium is the third most common element in the Earth´s crust, after oxygen and silicon; it remained undiscovered in its purest form until about 200 years ago. Since aluminium is very reactive chemically, it is not often found as a native specimen, it occurs naturally as bauxite ore. Chemists perfected the extraction of pure aluminium from bauxite in the 19th century and its applications increased greatly. This metal is strong, durable, resistant to corrosion, and it has a great capacity to be formed into nearly any shape.
Aluminium began being very popular in the railroad industry, automobile, and aviation sectors. In the early 20th century, it started to become popular for architecture. Its strength and durability makes it an excellent construction material. In the 1930s, it reached its climax when it was used to build the Empire State Building! From sky scrapers, to sheds, aluminium is present in many types of buildings. The metal has become popular for structural applications, as well as for use in numerous building components such as windows, doors, curtain walls, roofing, and even decorative applications Some of its unique trends are:
- Sustainability
- Anti-Corrosion finishes
- Interior design
- Innovative doors and windows
- Durable roofing designs
Aluminium Pretreatment
Pre-treatment of aluminium is necessary in order to ensure good adhesion of powder coating to the aluminium surface, and for it to have an extra protective layer against corrosion. Changing the surface of aluminium involves cleaning to remove residual oil, oxide films and mechanically disturbed layers. Pretreatment is necessary to provide corrosion protection and modify the surface for enhanced adhesion of coatings or adhesives. There are three approaches to cleaning, and these provide a surface that is suitable for pretreatment.
- Alkaline spray or immersion
- Acid spray or immersion
- Acid electrolytic cleaning
The process of pretreatment is often integrated with a strip cleaning process, and a coating process. The pretreatment can either be an electrolytic process or a chemical process, to replace or change the oxide film in the aluminium.
Mechanisms of Aluminium Pretreatment
- Formation of a barrier layer restriction ion, water, and oxygen access to the substrate
- Chemical and mechanical stabilization of the native oxide film
- Improved bonding potential to subsequently applied coatings or adhesives
- Increase of surface area
Achieving the correct structure of the surface of aluminium can signify the difference between success and failure of the final product. The demand on pretreated surface has increased in order to have more control and minimize failure, coupled with increased competition and higher production speeds.
Pretreatment Lines For Sale
Riley Surface World regularly has paint pre-treatment lines for sale either via our Electroplating Plant Catalogue or extensive Degreasing and Cleaning Catalogue
Machines & equipment for sale
- Surface Treatment
- Cleaning & Degreasing
- Polishing & Belt Linishing
- Mass Finishing
- Ovens & Furnaces
- Process Cooling
- Shot Blasting
- Dust & Fume Extraction
- Air Compressors
- Rectifiers & Transformers
- Miscellaneous
- Latest Stock
- Special Offers
- Direct From Site Clearances
- Auctions
- Brand New Machines
- Available Immediately
- Sell Your Machine
Machine Alert
Get the latest machines emailed directly to you as they become available to buy online. Sign Up Now