The Life Cycle of a Solar Cell in Production
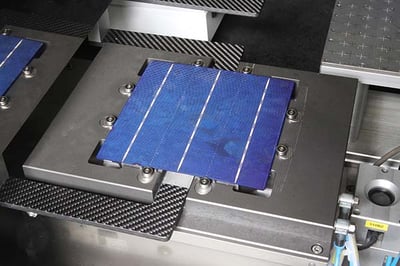
1. Purifying Silicon
Solar cells consist of silicon, which is the main component in natural beach sand. In order to use it, silicon has to be purified in an arc furnace at very high temperatures. The silicon is deoxidized through a process called Siemens Process. The impure part is cut off and 100% pure silicon rod is available to be used in the production process. In this process metallurgic silicon is transformed into tricloro silane gas, and with resolidification, you will get hyper pure polysilicon.
2. Ingots
After silicon is purified completely, the silicon is collected in the form of solid rocks, hundreds of these rocks are melted together at very high temperatures in order to form ingots in the shape of a cylinder. In the process of melting, atoms have to be perfectly aligned in the desired structure and orientation. Boron is added to the process, giving silicone positive electrical polarity. Mono crystalline cells are manufacture from a single crystal of silicon; they have higher efficiency in converting solar energy into electricity. Polysilicon cells are made from melting several silicon crystals together. After ingot has cooled down, it is grinded and polished, leaving it with flat sides.
3. Wafers to Solar Cells
To manufacture the wafers, With a Diffusion Machine, boron and phosphorus are added. Usually Boron for P type and Phosphorus for N Type. Then, the silicon ingot is sliced into thin disks, also called wafers. A wire saw is used for precision cutting. The thinness of the wafer is like a piece of paper. contacts are placed to connect each solar cell to another. After this, tin-coated copper strips are placed between the cells. Pure silicon is very shiny and can reflect up to one third of the sunlight, to prevent this, an anti-reflective coating of titanium dioxide or silicon oxide are put on the cell.
4. Solar Cells to Panels
After these steps, the solar cells are soldered together, using metal connectors to link the cells. Solar panels are made of solar cells integrated together in a matrix-like structure.
After the cells are put together, a thin layer of glass is added on the front side, facing the sun. The backsheet is made from highly durable, polymer-based material. This prevents materials from entering the panel from the back.
5. Testing
Testing is carried out to ensure the cells perform as expected. Standard Test Conditions are used as a reference point.
BDS Solar Panel Test Cabinet
A BDS Solar panel testing cabinet designed to heat soak test solar panels over an extended period. Radium daylight bulbs are used to create daylight testing conditions needed for solar panel testing.
- Stock No
- MA699
- Category
- Miscellaneous
- Model
- BDS Twin Bulb
- Year of Manufacture
- c.1998
- Capacity
- 4000W
- Process Application
- Heat Soak Solar Panel Testing
- Other Info
- Approx. Panel Sizes 900 x 450 (up to 6)
- Condition
- Seen working by RSW, Good Condition, Seen powered at RSW
- Sold As Seen Price [?]
- £ Login or Register for price.
Machines & equipment for sale
- Surface Treatment
- Cleaning & Degreasing
- Polishing & Belt Linishing
- Mass Finishing
- Ovens & Furnaces
- Process Cooling
- Shot Blasting
- Dust & Fume Extraction
- Air Compressors
- Rectifiers & Transformers
- Miscellaneous
- Latest Stock
- Special Offers
- Direct From Site Clearances
- Auctions
- Brand New Machines
- Available Immediately
- Sell Your Machine
Machine Alert
Get the latest machines emailed directly to you as they become available to buy online. Sign Up Now