What Does Chemical Milling Offer to the Manufacturing Industry?
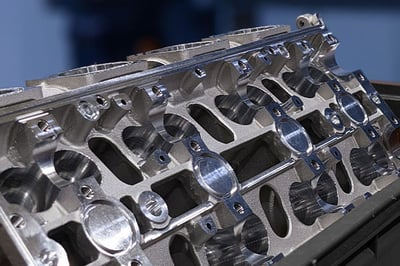
A surface finishing method with links dating back to before the 19th century, Chemical Milling (also well known as chemical etching) is a finishing technique most known for surface finishing metal components. An established finishing method in manufacturing for the ability to surface treat metal, plastic and composites, it is frequently used in the aerospace, electronics, medical and automobile industries.
Another industry where chemical milling has become popular is additive manufacturing (3D printing). An advancing industry greatly benefiting from this process's capabilities, find out more in our article Uses for Chemical Milling in Additive Manufacturing.
Continue reading to learn about the process of chemical milling and its potential to offer across the industry.
What Materials Are Suitable for Chemical Milling?
Most known for surface finishing metals such as aluminium, titanium, nickel, steel, copper and their alloys, chemical milling is able to provide these metals with additional properties to improve their performance, structure and appearance.
Plastics and composites resistant enough to withstand the etchants are also suitable for chemical milling. Plastics like polyimides & polyetherimides, these low energy plastics have low surface energy resulting in their high resistance. While for composites, carbon fibre is known for its strength (it can be ten times stronger than steel). These durable characteristics make these materials especially chemically resistant to tolerate the etchants.
Playing to the strengths of the process, especially since the etchant will react with all the exposed (and difficult to reach) areas and causes no stress to the parts during the process, chemical milling is perfect for complex and delicate components. Able to reach more confined areas other machinery methods can’t do without the risk of breaking slender components like mesh or thin panels.
What is Chemical Milling Used For in Surface Finishing?
One of the most in demand reasons for the method is for surface milling the component. As explained in more detail in our additive manufacturing & chemical milling article, the purpose of this is to remove material from the components. The objective is typically to maintain the general shape of the part while reducing the weight and eliminating any unwanted material.
Chemical milling can be partially applied with the use of chemical resistant masks so the process is only carried out on selective areas.
Branching off from surface milling, you get taper milling which focuses on components with a repetitive shape and difficult shapes to finish with mechanical finishing. Applicable for metallic parts in the form of mesh, sheets, bars and tubes and shaped parts such as airplane structures, this more automatic technique is for refining the surface at a uniform rate for consistent results.
Focusing on the result to enhance the appearance, decorative pattern milling relies on applying a mask to achieve a specific look. Able to be applied with a screen, like when screen printing a t-shirt, the mask is applied to a component with a flat surface for the best results before being submerged in the etchant.
Machinery for Chemical Milling
The shape, material, and desired finish determine the machinery needed, ranging from a small unit to a complete treatment line.
An example of the smaller plant includes spray etching machines used to etch the metal plates frequently seen on machinery and vehicles. Able to be as small as an office printer and featuring a small conveyorised track, these machines can produce wear resistant signage like a printer prints paper.
Looking at the opposite end with large scale treatment lines, these are the multi-stage ‘compact’ lines that include a series of tanks for submerging the components, as typically seen with surface milling. Made for the large components in the aerospace and automobile industries, the parts are loaded into an automated transporter that slides above the tanks. Dipping the parts in a cycle to clean, etch, neutralise and dry, frequently repeating the etching and neutralising stages with the same or different etchants.
A key feature of these machines is the processing tanks as the material of the tank determines what etchants can be used. Able to be made of plastic and metal depending on their chemical requirements.
Benefits of Chemical Milling in Manufacturing
A go-to method for surface finishing strong and resistant materials, the advantages chemical milling can bring to all industries that use these materials include:
- Precision and Complex Geometries - Can surface treat complex forms with ease at a uniform rate.
- Cost Effectiveness - There is no need for expensive tooling with a quick production time.
- Material Versatility - Even though the materials need to be of high resistance, there is still a large variety of metals, plastics and composites compatible for chemical milling.
- Stress-Free Processing - No risk of damage or warping delicate parts.
- Fast Prototyping and Short Lead Times - Quick production times make for quick prototypes.
- Reduced Material Waste - As the material is dissolved, you don’t get leftover cuttings.
- Surface Finishing and Texture Control - The precision of the method also allows for control of the surface textures from matte to polished to textured.
- Batch Consistency and Reproducibility – Once the process parameters are selected, the cycle can keep reproducing the same finish.
Importance of Chemical Milling in the Manufacturing Industry
A surface finishing process made for handling the most resistant of materials, chemical milling is able to process what can become the most beneficial of components. Used in industries that demand quality finishing, such as aerospace, defence and medical, precision is a must and this method can reproduce the same result every time.
In demand for a reason, Chemical Milling is used across industries for its wide range of purposes, meaning we’ll continue to see it for many years to come.
Riley Surface World's Direct From Site Service regularly sells process and chemical milling lines so register as a member to be told when one is available.
Machines & equipment for sale
- Surface Treatment
- Cleaning & Degreasing
- Polishing & Belt Linishing
- Mass Finishing
- Ovens & Furnaces
- Process Cooling
- Shot Blasting
- Dust & Fume Extraction
- Air Compressors
- Rectifiers & Transformers
- Miscellaneous
- Latest Stock
- Special Offers
- Direct From Site Clearances
- Auctions
- Brand New Machines
- Available Immediately
- Sell Your Machine
Machine Alert
Get the latest machines emailed directly to you as they become available to buy online. Sign Up Now