What is Abrasive Blasting?
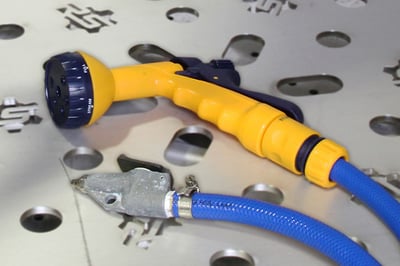
Abrasive blasting is one of the most effective and efficient tools for preparing surfaces of manufactured parts for all sorts of processes such as polishing, galvanizing, electroplating, and welding. During abrasive blasting, pressurized air or water is used to propel abrasive media against a surface to make a rough surface smooth, make a smooth surface rough, shape a surface, remove contaminants, clean or prepare, or finish a surface.
This flexibility also makes it useful for remanufacturing, repairs, renovation and handling parts that fail quality control.
Shot blasting is one of the most common types of techniques. Shot blasting is a surface treatment technique that uses particulate grains propelled under high velocity. The process of shot blasting is an effective solution to clean, strengthen (peen) or polish metal. It is used in almost every industry that uses metal, including aerospace, automotive, construction, foundry, shipbuilding, rain, and many others.
How does Abrasive Blasting Work?
The main types of abrasive blasting systems are:
- Suction Blasting: The entry point to blasting using air to suck media into the blasting nozzle
- Pressure Blasting: A higher performance version of dry blasting where pressure forces media through the machine
- Wet Blasting: The media is mixed with water to provide a different kind of blasting finish to dry blasting
- Airless Blasting: The media is thrown against the surface often using a spinning disc to accelerate it and not a stream of air.
ex. of a pressure blasting system
Types of Abrasive Blasting
There are different terms referred to when relating to abrasive blasting, and they normally refer to the type of media being used, the method, or a combination of both. The right type of blasting should be selected based on your specific needs.
Some regions and countries use these terms as umbrella generic terms to refer to all abrasive blasting, such as “sand blasting” or “shot blasting” and once you approach the detail refine the terms to the correct process.
Silica blasting, Sandblasting or Grit blasting
Blasting with mineral sands containing crystalline silica. Dust is generated by durn blasting as the media breaks up and the surface is cleaned. This is particularly an issue with silica sands so special media is used such as aluminium oxide, garnet, magnesium sulphate or kieserite
Shot Blasting
Shot Blasting is often used in the process of removing paint and rust from steel surfaces. The shot can be made from materials like steel grit, copper shot, or aluminium pellets. The variety of granules on this abrasive makes it ideal for fast cutting, leaving a smooth surface. The size and hardness of the shot material will dictate how much surface removal of the material being cleaned will occur.
Airless/Wheel Blasting
The propulsion method is an important part of the shot blasting process and impacts the machine size, cost and performance. Wheel blasting uses a centrifugal blast wheel that shoots media onto a surface at high velocity. This knocks the surface free of debris and other material. The shot media varies loads into a hopper that feeds the blast wheel.
Wheel Blasting/Shot Peening
Shot peening is known for hardening the surface of metal components to prepare them for use. It uses the same principle as abrasive blasting with a slightly different aim.
Glass Bead/Bead Blasting
This method uses glass beads at lower air pressure. Bead blasting is used in cleaning, deburring or peening metal surfaces. The smaller the glass beads, the smoother the finished surface will be. This method is great for matte and satin finishes and is better for cleaning a surface without leaving much of an impression.
Plastic Abrasive
Less aggressive media than other types of abrasives, it is great for blasting on softer substrates. Commonly used for plastic components and mould cleaning.
Soda Blasting
Sodium bicarbonate particles are used as the abrasive material; they are propelled onto surfaces using compressed air. Applications of soda blasting include automotive restoration, rust removal, wood cleaning, graffiti removal, and cleaning of boat hulls.
Advantages of Abrasive Blasting
- Eco-friendly: abrasive blasting is more environmentally friendly than chemical cleaning.
- Provides higher production rates, wider abrasive selection and better blast pattern accuracy
- The finished surface becomes free of chemical deposits, scales and dust.
- Facilitates the formation of a permanent bond between the protective coat and the shot blasted surface.
- Increases longevity and durability of protective surface coats as it adheres better to the cleaned and scale-free surface.
Riley Surface World offers a wide range of shot blasting equipment of different sizes, functions and shapes to suit your needs. Rileys is the world´s leading live and online marketplace for new and used industrial treatment machinery.
Machines & equipment for sale
- Surface Treatment
- Cleaning & Degreasing
- Polishing & Belt Linishing
- Mass Finishing
- Ovens & Furnaces
- Process Cooling
- Shot Blasting
- Dust & Fume Extraction
- Air Compressors
- Rectifiers & Transformers
- Miscellaneous
- Latest Stock
- Special Offers
- Direct From Site Clearances
- Auctions
- Brand New Machines
- Available Immediately
- Sell Your Machine
Machine Alert
Get the latest machines emailed directly to you as they become available to buy online. Sign Up Now