Why You Should Choose High-Velocity Fuel Coating (HVOF)
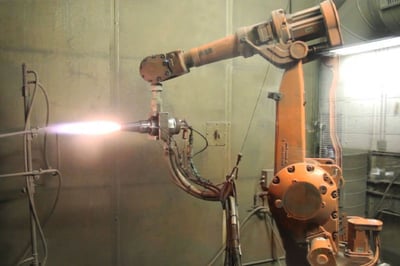
High Velocity Oxygen Fuel coating is a thermal spray coating process that is used to improve or restore a component´s surface. This surface engineering technique better enables life extension of equipment by increasing erosion, wear resistance, and corrosion protection. This process was developed in the 1980s, and is a subset of thermal spraying.
Using HVOF coating technique allows the application of coating materials such as metals, alloys, and ceramics to produce a coating of exceptional hardness, outstanding adhesion to the substrate material and providing substantial wear resistance and corrosion protection.
Advantages of Using HVOF Coating
- Enhanced protection against wear, corrosion, fatigue, oxidation and high temperatures.
- Lower oxide content due to less in-flight exposure time.
- Retention of powder chemistry due to reduced time at temperature.
- Smoother as sprayed surface due to higher impact velocities and smaller powder sizes.
- Higher hardness due to less degradation of carbide phases.
- Thicker coating.
- Reduced costs.
- Improved performance and electrical properties.
- Enables components to operate in higher/lower temperatures and harsh chemical environments.
- Improved efficiency and improved life of mating components.
Application & Materials
Thermal spray coating is an attractive technique because it offers a wide choice of materials and processes that have a reduced impact on the environment when compared to conventional processes. HVOF coating materials that are available for thermal spray coating include metals, alloys, ceramics, plastics and composites.
- Valve gates & seats,
- Mandrels,
- Ball valves,
- Rock Drill Internals,
- Pump impellers and internals,
- Sub-sea infrastructure components,
- Landing gear,
- Gas Turbine Components.
Process Details
HVOF coating material is heated and accelerated by a gas stream to a component´s surface, to attain better properties. The gas stream is produced by mixing and igniting oxygen and fuel (gas or liquid) in a combustion chamber and allowing the high-pressure gas to accelerate through a nozzle. A powder is introduced into this stream where it is heated and accelerated towards a component´s surface. The resulting thermal spray coating consists of thin overlapping platelets.
If interested in machinery for high-velocity fuel coating, visit our Associated Process Plant & Equipment for our available stock or make an enquiry at +44(0)1922 45 8000
Machines & equipment for sale
- Surface Treatment
- Cleaning & Degreasing
- Polishing & Belt Linishing
- Mass Finishing
- Ovens & Furnaces
- Process Cooling
- Shot Blasting
- Dust & Fume Extraction
- Air Compressors
- Rectifiers & Transformers
- Miscellaneous
- Latest Stock
- Special Offers
- Direct From Site Clearances
- Auctions
- Brand New Machines
- Available Immediately
- Sell Your Machine
Machine Alert
Get the latest machines emailed directly to you as they become available to buy online. Sign Up Now