Thermon Heating Systems Hazardous Environment Catalytic Infrared Drying and Curing Oven
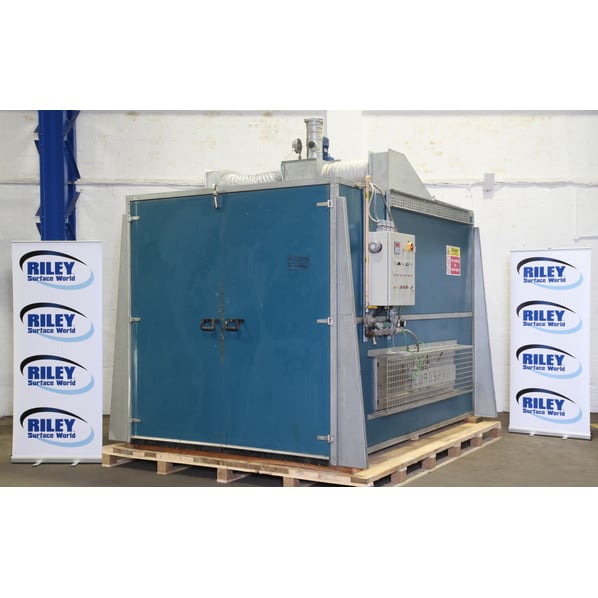
- Stock No
- OZ2079
- Manufacturer
- Thermon Heating Systems
- Model
- Eurospray
- Serial
- 227201
- Condition
- Excellent Condition
- Internal Size (WxDxH mm) [?]
- 2050x 3120 x 2050
- Max Temp
- 40°c - see spec below
- Other Info
- Hazardous environment, curing/drying
- Location
- Our Central Warehouse, Aldridge, UK
- Weight (kgs)
- 1450
- External Dimensions (WxDxH mm) [?]
- 2620 x 3400 x 3020
- Delivery Your delivery options
Description
Explosion proof Infrared Catalytic Heaters, mounted into a tunnel style oven, are flameless gas heaters that are designed to run on clean dry natural gas or propane. Ideal for heating in a hazardous environment and for curing, stoving or a drying processes.
Features.
- Cata-Dyne manufactured Explosion-Proof Gas Catalytic heaters.
- The system consists of a robust enclosure of modular panel and box section design.
- Full width opening swing doors at each end with automatic final closers.
- Air circulation fan and assisted exhaust venting.
- Control panel.
- Catalytic infrared emitters and gas train (Currently arranged for Propane can be configured for natural gas).
- Stainless steel is used through out the internals of the enclosure to assist in the reflection of the infra red radiant heat around the product to be dried.
Details.
- Internal Enclosure measurements are 3200mm in length , 2050mm Width, and 2180mm in height.
- Fan Motor 2.2Kw for air circulation and assisted exhaust venting.
- 950 Rev / Min.
- 5.5A
Gas heater.
- CE / ATEX approved.
- Model WX18X72.
- S/no 227201.
- Fuel type LPG. Can convert to natural gas.
- Starter 240V 12.1A 50hz.
- Input max 45000 BTU. (13.179 kW)
Explanation of operation
What it is designed to do
Designed to dry/cure solvent or water based coatings quickly and with full cure unlike hot air ovens which dry the coating but full cure can take several days. Coatings include but are not limited to: stains, lacquers, primers, top coats, preservatives, 2 pack coatings etc.
How It can only heat what it can see
Infrared gas ovens work on medium to long wavelength in direct lines which is why the ovens are finished in polished stainless steel so that the infrared is reflected to all surfaces of the product being cured.
Example
A example is a large manufacturer of pine toilet seats used to lacquer the finished seat and had to leave them on racks to air dry for 24 hours even after this time they had problems with the protective packaging sticking to the coating (lacquer). They tried a hot air oven but couldn’t use to much hot air temperature to dry the coating as it effected the final finish. After trials they purchased a Quick-cure oven, now they coat the seats – rack them after 20 minutes in the oven (20 minutes is the time taken to spray and rack enough product to fill a oven), the coating is cured and can be sanded or packed (after a cool down period of 10-20 minutes. They went from 25% plus complaints and returns from customers to zero (no problems with packaging sticking or marking the product) and didn’t need to store product for 24 hours before shipping out.
Not suitable for stoving/powder
Due to the ovens being low temperature ovens they are not suitable for stoving or powder curing (these require temperatures of 100 to 200 plus deg C)
Air circulation etc.
The oven uses a re-circulation fan to even out the surface temperature on the products, air is passed over the faces of the infrared emitters (heaters) and collects the convection heat on the face of the heater caused by the catalytic reaction this warmed air then is recirculation round the oven to even out the temperature and assist the curing/drying process.
Why it can’t be upgraded : Thickness of insulation
The construction of the oven and insulation is only suitable for this type of oven. On a infra red oven the structure does not get hot unlike a hot air oven where everything inside the hot air oven has to get to the same temperature as the coating.
Infrared emitters
Catalytic heaters rely on a catalytic reaction to generate heat. The catalytic reaction is flameless, and it involves the use of a gas and a platinum catalyst. Catalytic heaters are very effective because they rely on a platinum catalyst to speed up the rate of the reaction. Since the heater is efficient, there are higher emissions of steam, carbon dioxide and heat. The catalytic heaters produce a slow combustion which translates into lower emissions of pollutant particles. What is the efficiency of an infrared catalytic heater? An infrared catalytic heater has an efficiency of 98%. This means that, since gas is the primary source of energy, 98% of the gas fuel is transformed into heat. This shows that there is very little wastage and loss of energy when using an infrared catalytic heater.
When compared to more conventional systems, the process times are reduced by 65%, the area required is reduced by up to 50%. Gas catalytic infrared emitters will convert both natural or propane gas into infrared energy by using a specialised platinum catalyst.
By-products are water and carbon dioxide. The energy of infrared is emitted continuously in a 180° spherical axis. It is across the entire face of the heaters.
How do Infra-red ovens work?
When they are paired on opposite walls of the oven, this pattern will provide complete coverage across that part of the window and will allow for a diffused heat that is easily controlled. The wavelength of catalytic gas infrared will vary with the percentages of power output.
Maintaining lower temperatures require less gas and will produce longer wavelengths, allowing for extended dwell and slower reaction times, without it overheating.
With higher outputs, infrared wavelengths become denser, creating a medium wave emission. It will require a slightly higher percentage of gas output, and it is suited more towards rapid response needs, for instance, pre-heat, gel or drying applications.
An intuitive Gas Pulse System regulates the output percentages. Its recipe capable, HMI and PLC provide the GPS information that controls temperature through a series of LOW and HIGH gas pulses, monitoring the platinum reaction
Additional files
Photographs taken prior refurbishment. Our refurbishment service is not available on all machines.
Machines & equipment for sale
- Surface Treatment
- Cleaning & Degreasing
- Polishing & Belt Linishing
- Mass Finishing
- Ovens & Furnaces
- Process Cooling
- Shot Blasting
- Dust & Fume Extraction
- Air Compressors
- Rectifiers & Transformers
- Miscellaneous
- Latest Stock
- Special Offers
- Direct From Site Clearances
- Auctions
- Brand New Machines
- Available Immediately
- Sell Your Machine
Machine Alert
Get the latest machines emailed directly to you as they become available to buy online. Sign Up Now