Oxford Applied Research Solar Vacuum Laminator
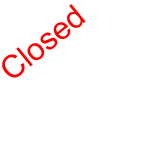
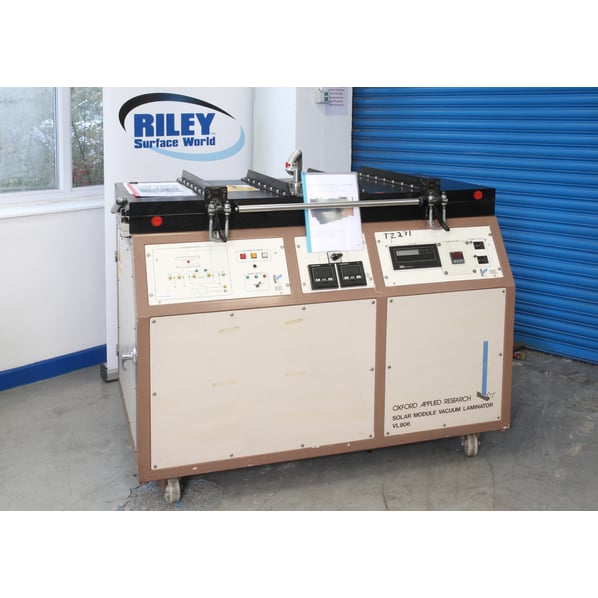
Auction
- Our partner auctioneer is
- Peaker Pattinson
- Part of an Auction
- Clearance Auction
- Lot ID
- TZ271
- Manufacturer
- Oxford Applied Research
- Model
- Laminate All vl 806
- Year of Manufacture
- 2011
- Serial
- F1079/ SF2225
- Condition
- From a working environment
- Capacity
- 1200 x 600 tbc
- Process Application
- Laminate and Cure
- Other Info
- Mobile heavy duty build qualtiy
- Location
- Clearance Auction
- External Dimensions (WxDxH mm) [?]
- 1450 x 900 x 1055
- Delivery Your delivery options
Description
Oxford Applied Research Solar Vacuum Laminator
System Overview
Vacuum Lamination
The laminating process is performed in a vacuum chamber which is divided into upper and lower parts by means of a diaphragm.
lower part contains a heated platen on which the panel to be laminated is placed. The process is illustrated in figure 2.1 and typically consists of the following steps
(i) The panel is placed in the chamber, the chamber is closed and both sides of the diaphragm are evacuated
(ii) The panel is heated to the correct temperature.
(iii) Atmospheric pressure is admitted to the upper part of the chamber, forcing the diaphragm to press onto the panel
( v) The lower part of the chamber is let up to atmosphere.
(v) A high temperature cure process, followed by cooling may then take place, or the panel is removed
Operating modes
The system can be operated in any of three modes.
Mode 1 Automatic Laminate
Mode 2 Automatic Laminate and cure
Mode 3 Manual operation
Mode 1 - The platen is held at a constant temperature Both sides of the chamber are pumped down and when the pre-set pressure is reached in both parts of the chamber, the pumping time is started. At the end of time, the upper part of the chamber is opened to atmospheric pressure and the compression time is started. At the end of time the chamber is let up to atmosphere and the cycle is complete.
Mode 2 - The platen is initially held at a constant low temperature. Both sides of the chamber are pumped down to the pre-set pressure. At point the pumping time is started, and also the temperature is ramped up, at a rate to the laminate temperature. At the
end of this time, the compression phase is started and at the end of this phase the chamber is vented. In parallel with the vacuum cycle
the temperature controller holds the laminate temperature for a dwell time and then ramps up at a rate to the cure temperature. After a further dwell time the temperature controller reduces to the set point, which starts the cooling system.
Mode 3 -The vacuum system is controlled directly from the mimic panel by the operator
Vacuum chamber
The vacuum chamber is an aluminium vessel consisting of two parts hinged together like a clam shell. This allows the chamber to be opened to insert and remove panels to be laminated. While open, the upper shell is supported by gas-filled struts. Both shells have stiffening ribs to prevent them distorting under the pressure of the atmosphere. The upper shell has the glass-fibre reinforced silicone-rubber diaphragm, which divides the chamber into two parts. The lower shell contains the heated platen.
Print / Download Oxford Applied Research Solar Vacuum Laminator Datasheet
Additional files
Solar Panel Wafer Manufacturing Process Equipment
Auction Lots Descriptions and photographs are provided in good faith but may not be correct. It is the Customer's responsibility to ensure that the machinery is fit for the purpose for which it is purchased and safe for the purpose of use at work via physical inspection. All sales are deemed to be 'as inspected' and 'as is, in situ' even if the customer has waived the right to inspect.
Machines & equipment for sale
- Surface Treatment
- Cleaning & Degreasing
- Polishing & Belt Linishing
- Mass Finishing
- Ovens & Furnaces
- Process Cooling
- Shot Blasting
- Dust & Fume Extraction
- Air Compressors
- Rectifiers & Transformers
- Miscellaneous
- Latest Stock
- Special Offers
- Direct From Site Clearances
- Auctions
- Brand New Machines
- Available Immediately
- Sell Your Machine
Machine Alert
Get the latest machines emailed directly to you as they become available to buy online. Sign Up Now