Surface Dynamics Automated 4 Gun Twin Axis Shot Peening System
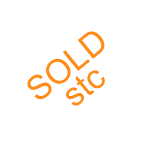
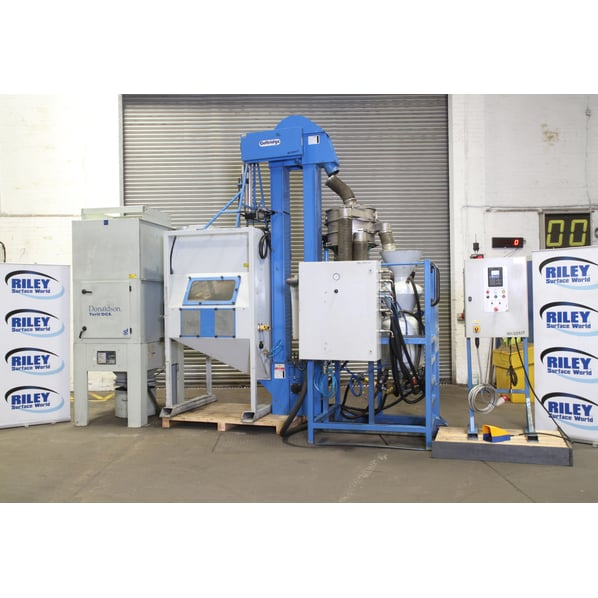
- Stock No
- SB957
- Manufacturer
- Surface Dynamics
- Model
- ALOX 180 Auto Blasting
- Year of Manufacture
- 2007
- Serial
- 6223/000001
- Condition
- Excellent Condition, Current Model, Seen powered at RSW
- Work Envelope (WxDxH mm) [?]
- 1010 x 700 x 1130
- Work Handling Method
- Manual Load Rotary Table 4 x Recip' Guns
- Other Info
- Programmable auto Blast Process
- Location
- Our Central Warehouse, Aldridge, UK
- External Dimensions (WxDxH mm) [?]
- 2140 x 1390 x 3750
- Delivery Your delivery options
Description
This blasting system was originally designed for the automatic cleaning of jet engine aerofoil blades but with potential countless other uses.
The blast cabinet includes a powered turntable and fitted to a linear actuator are 4 blasting nozzles. Media recovery from the cabinet to the stack is via a gravity fed bucket elevator. The stack which includes a vibratory deck media separator and twin pot continuous blast system.
Blast Cabinet
- The fabrication of the cabinet comprises of a box section steel with 3mm thick steel sheet and 3mm thick rubber internal lining. The front panel is fitted with a safety glass viewing window protected by a fine mesh cover and internal fluorescent lighting. Manual loading door is to the left hand side.
- Airborne dust is extracted through the side wall of the booth to the dust collector via flexible ductwork Used media collects in the sump and recycles via the bucket elevator back to the media feed hopper.
- The work is mounted into the tooling holder on the rotary turntable. Loading is facilitated by bringing the work car fully forward. The work car has a rotary drive motor/gearbox with electronic speed control powering the work holder, the speed control knob is mounted on the control panel.
- A flanged bearing takes the load through the (hollow) driveshaft. An air purge supply is connected to the bottom of the driveshaft the air stream emerging into the tooling holder is designed to minimize the ingress of media and debris into the cooling passages of the work.
- Four vertically tracking blast nozzles are connected to two actuator arms and mounted on adjustable fixtures, two on each back/side of the work. All the nozzles are tungsten carbide internally with threaded fittings for ease of hose or nozzle replacement.
- The actuator arms holding the tracking nozzles pass through the roof of the cabinet and they are clamped to the carriage of the linear actuator and guide-rail system which is mounted securely on the roof of the cabinet. The carriage slides up and down the rail on ball bearings. A ‘home’ limit switch mounted externally to the actuator allows sensing position of the actuator start point. Bellows seals around the actuator arms are fitted internally to the cabinet to prevent excess media and debris from escaping to the roof area of the cabinet.
- The actuator is a belt driven device, powered by an AC motor/gearbox with variable speed control. The speed control knob is found on the control panel.
- Loading access is provided into the booth through a wide-opening, rigid door fitted with heavy-duty lever-latches and hinges. The door is fitted with a safety interlock, to prevent operation of the machine when open.
- Media filling - is achieved by introducing it into the sump of each cabinet (through the main loading door). The bucket elevator must be running during top-up filling. The machine should be filled only until the media-high indicator lamp illuminates, this is sited just below the cabinet door and triggered by the internal paddle switch.
Recovery/Blast Stack
- Recovered media is lifted from the booth by a 1.5 kW bucket elevator. This recycles to the vibratory separator which removes undersize and oversize media and debris. The reusable media passes through to the pressure blast system, which feeds the booth nozzles. The media separator is a dual deck 24” unit, the oversize media is rejected to the waste bin and undersize particles are carried away to the dust extractor. The coarse mesh screen is #20, fine mesh #180/200 grade.
- The cyclone separator accepts the media and recovery air flow from the booth and separates the re-useable media from the dust laden air which, is drawn off to the dust collector.
- The degree of separation can be controlled by the setting of the air wash eductor from within the pneumatic cabinet and/or by closing the adjustable air vents on the side of the cyclone/storage hopper. The position of the air wash cone is preset during commissioning to retain clean re-useable media and transfer the undersized particles to the dust collector. However, should the eductor pressure adjustment be insufficient to prevent carry over of media into the dust collector, the height may be adjusted. This adjustment may be required when changing to a media with a very different specific gravity i.e. heavier or lighter.
- The re-usable media passes from the cyclone separator onto a vibrating oversize debris screen which removes any large particles or debris. The re-usable media then drops into the storage hopper ready for re-use.
Media
- The original media was a 'cut wire shot' media.
Produced by cutting steel wire into lengths equal to the wire diameter, CUT WIRE is a mono grain size abrasives with a good service life at high blasting velocity. Conditioned CUT WIRE is mainly used in shot peening applications.
Some typical applications include Suspension springs, valve springs, gears, shafts, car bodies, valves, fittings and aerofoils.
Control Panel
- Allen-Bradley PanelView 300 controller.
- Turntable speed controller.
- Actuator speed controller.
- Extractor fan stop/start.
Load Conveyor (Guttridge)
- Guttridge made media loading conveyor, 3750mm tall.
- Bucket elevator.
Sieve Separator (Russell Finex)
- Vibratory separator.
- Triple outlet media sizing/grading.
Automated Blast Cabinet (Surface Dynamics)
- Mild steel construction.
- Rubber lined.
- Glass viewing panel.
- Left hand side opening door.
- 4 Blast guns.
- Pneumatically operated vertical gun movement.
- Forward and backward moving loading trolley with powered rotational drive spigot.
Dust Extractor (DCE Unicell)
- Unicell C10-3K5.
- Modular construction, self contained. Size 1375mm x 1460mm x 2850mm.
- 2.2kW motor.
- Filter area 10m².
- 2 Filters.
- Reverse pulse jet cleaning for continuous use.
Pressure pot (AJ Metal Products)
- A Class 2 Cyclone and pressure pot.
- 100Ltrs.
- No: 25561 9.5 bar .
- tmax/min 85/-10 degc.
- Housed in a frame below the vibratory sieve.
Sizes and weights for SB957
Main body 1400 x 1400 x 2800
Elevator 1100 x 600 x 3750 combined weight 1000 KG
Pressure pot and frame 1800 x 1600 x 2130
Eco separator 1200 x 1200 x 1100 combined weight 1000 KG
Control panel 800 x 1200 x 1950 100 KG
Dusty 1400 x 1500 x 2820 450 Kg
What is Shot Peening?
A process widely used in manufacturing mechanical parts, shot peening is known for hardening the surface of metal components to prepare them for use. As the life of these parts will often be repetitive & stressful, fractures and breaks are liable. Shot peening is used to reinforce the surface of the metal, strengthening the fatigue resistance.
Shot peening is a cold work process when a media in the form of small circular objects is shot at a metal subject with enough force that results in a small dent to the surface. The media can be metal, glass or ceramic, with multiple of the small ball-bearing sized objects used to create multiple tiny indentations to the surface. As each impact indents the surface, the directly targeted area will cave in with surrounding (softer) material pushing to the sides into the compression range. Because lots of media is aimed at the area, the compression range will be repetitively hit causing the overall area to be compressed & encased in a compressively stressed layer.
Commonly used in the medical, aerospace & automotive industries, shot peening is used for an extensive range of items such as gears, springs, rods, crankshafts, pistons, drill bits, propeller shafts, turbine blades, epidural gear & much more.
Print / Download Surface Dynamics Automated 4 Gun Twin Axis Shot Peening System Datasheet
Photographs taken prior refurbishment. Our refurbishment service is not available on all machines.
Machines & equipment for sale
- Surface Treatment
- Cleaning & Degreasing
- Polishing & Belt Linishing
- Mass Finishing
- Ovens & Furnaces
- Process Cooling
- Shot Blasting
- Dust & Fume Extraction
- Air Compressors
- Rectifiers & Transformers
- Miscellaneous
- Latest Stock
- Special Offers
- Direct From Site Clearances
- Auctions
- Brand New Machines
- Available Immediately
- Sell Your Machine
Machine Alert
Get the latest machines emailed directly to you as they become available to buy online. Sign Up Now