Machines & equipment for sale
SPX Blue M Sealed Chamber Controlled Atmosphere Industrial Laboratory Oven with Process Cooling.
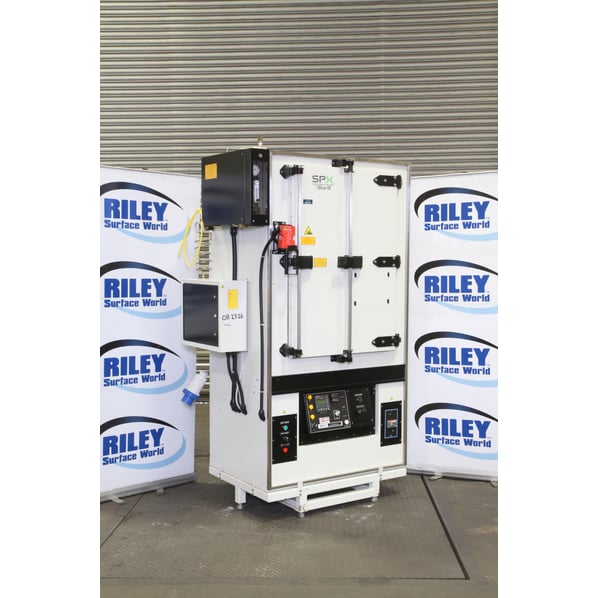
SPX Blue Oven
- Stock No
- OB2326
- Manufacturer
- SPX Blue M
- Model
- DCI-336-CY-F4-CE
- Year of Manufacture
- 2013
- Serial
- 99961-05
- Condition
- Excellent Condition, Current Model
- Internal Size (WxDxH mm) [?]
- 635 x 505 x 960 (310 Litre)
- Max Temp
- 350°C
- Other Info
- Indirect Heat, Inert Gas and Cooling
- Location
- Our Central Warehouse, Aldridge, UK
- Weight (kgs)
- 400
- External Dimensions (WxDxH mm) [?]
- 1295 x 870 x 2230
- Delivery Your delivery options
Description
The Blue M series of Inert Gas Model DCI ovens are utilized for processing materials in an inert atmosphere using a gas injection system. An inert atmosphere prevents oxidation from occurring on the product and eliminates the capability of oven air from supporting a flame. New Price today £50,000.
Features
- 240Volt single phase power.
- Max temp 350°C.
- 304 Stainless steel chamber.
- Powder coated easy clean external framework.
- 101mm thick none asbestos fibreglass.
- Initial purge cycle.
- Heating and cooling cycles.
- Variable speed blower wheels.
Operation
- In this model, an initial high purge cycle will remove oven ambient air before heating is allowed to begin. A constant low flow of gas will then be maintained during the heating and cooling cycles. Inert gas flow and chamber pressure are monitored and regulated with various instruments on the gas control panel.
- Precise temperature control is achieved with the Watlow F4 Temperature Controller. All control equipment is mounted in a Type NEMA 1 control cabinet.
Airflow
- Inert gas is injected into the conditioning plenum below the inlet of the blower wheel. The gas mixes with circulating process air and is forced through the heaters and the water-cooled cooling coil, and is discharged up into the right side duct wall.
- Conditioned air enters the workspace through either pierced or semi-pierced openings over the entire height and depth of the workspace. The air flows in a horizontal pattern from right to left to condition the product and exits through pierced openings in the left side duct wall. Process air returns to the conditioning plenum and the cycle continues.
- To insure that an overpressure condition does not develop within the chamber, a vent port is installed in the chamber ceiling. A Pressure Relief Valve PRV is installed on the vent port atop the chamber. PRV will automatically open when chamber pressure reaches 0.5 PSI not to exceed 1.0 PSI. Slight chamber pressures up to 0.5 PSI will not adversely affect the integrity of the oven door seal.
Heating
- The heating of the oven is achieved by recirculating oven air through open-air heavy gauge nichrome wire heater elements mounted in the conditioning plenum, 8kW.
- Each element is configured in a serpentine pattern within a cylindrical stack and supported by ceramic disks. The number of heater stacks used varies between one and three, depending on oven size and heating requirements.
- The heaters are isolated from the workspace so that no direct radiation can occur.
- A time proportioned type output of the main controller is used to trigger one or more solid state relays to conduct and provide power to the heater(s).
Cooling
- For enhanced cooling or when the chamber is sealed, an aluminium finned water cooled coil is used. The coil is located in the conditioning plenum, circulating processed air to cool as it flows through the coil. A city water type supply is required with a maximum temperature of 75°F.
- It is important to remember to pipe the drain line to an open bell-type drain.
- With the standard non-profiling type controller, a Cooling Switch located on the main control panel is normally used to energize a Water Cooling solenoid valve to permit cooling water to flow through the coil.
Equipment
- Manuals/data sheets are available.
- Allen Bradley program controller.
- Watlow F4 temperature controller.
- Watlow EZ high limit controller.
- Variable speed drives.
- Differential pressure switches.
- Allen Bradley safety door interlock switch.
- Chamber pressure gauge.
- Multiple inlet solenoid valves.
- Series 3510 trace oxygen transmitter/analyzer.
Uniformity/Conformity
- The original uniformity records are available on request.
- Uniformity tests conducted at 3 temperatures. 100°C, 80°C and 65°C
- A certificate of Conformity from the OEM is also attached.
Full service and spares are available through the U.K. agents.
Additional files
Photographs taken prior refurbishment. Our refurbishment service is not available on all machines.
Machines & equipment for sale
- Surface Treatment
- Cleaning & Degreasing
- Polishing & Belt Linishing
- Mass Finishing
- Ovens & Furnaces
- Process Cooling
- Shot Blasting
- Dust & Fume Extraction
- Air Compressors
- Rectifiers & Transformers
- Miscellaneous
- Latest Stock
- Special Offers
- Direct From Site Clearances
- Auctions
- Brand New Machines
- Available Immediately
- Sell Your Machine
Machine Alert
Get the latest machines emailed directly to you as they become available to buy online. Sign Up Now
Close Menu