S G Nitriding Furnaces Bell Style, Controlled Atmosphere, Nitriding Furnace
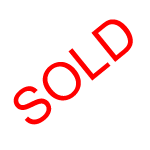
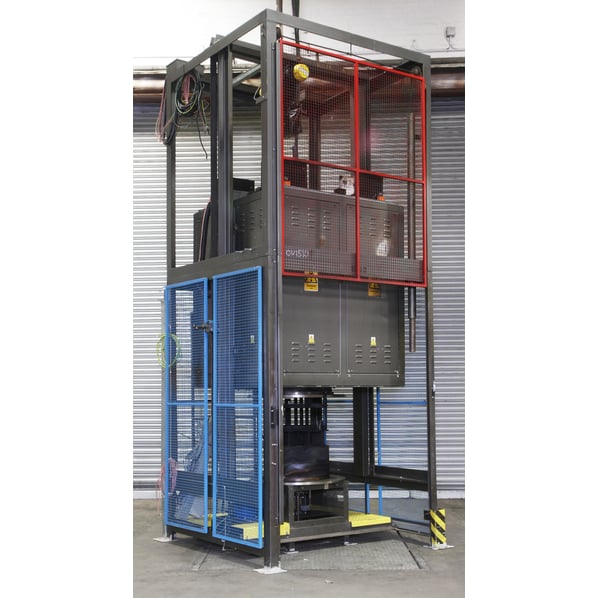
- Stock No
- OC2416
- Manufacturer
- S G Nitriding Furnaces
- Model
- Gas Nitriding Bell Furnace
- Year of Manufacture
- Ref 2016
- Serial
- 97 500A
- Condition
- From a working environment, Good Condition
- Internal Size (WxDxH mm) [?]
- Ø550 x 750
- Max Temp
- 1175°C
- Other Info
- New CSM 40mm Seal fitted in 2016
- Location
- Our Central Warehouse, Aldridge, UK
- Weight (kgs)
- 2500
- External Dimensions (WxDxH mm) [?]
- 2230 x 2300 x 4680
- Delivery Your delivery options
Description
The SG nitriding, bell style furnace has been specified and built primarily as a gas nitriding furnace operating under a monitored gas environment. But with its 1175°C temperature range, it is also suitable for a wide range of other heat treatments including; carburising, carbonitriding, annealing, brazing and nitrocarburizing.
This bell furnace is electrically heated with air/atmosphere circulation, 3 zone control, multi-programme capability, atmosphere control, integrated top hat hoisting and with a built in rapid air quench facility.
The technical specifications of this furnace include 300kg load capacity, 750mm carrier height, 550mm useful diameter and 1175°C degrees maximum temperature range.
This furnace is easily integrated into existing work processes and can be adapted at any time in line with evolving needs, easy to operate in full or semi automatic modes, and it has the highest quality combined with top performance.
Process Overview
Nitriding is a heat treating process that diffuses nitrogen into the surface of a metal to create a case-hardened surface.
The process is commonly used on low-carbon, low-alloy steels. They are also used on medium and high-carbon steels, titanium, aluminium and molybdenum.
Nitriding can be even be used to generate unique duplex microstructure (Martensite-Austenite, Austenite-ferrite), known to be associated with strongly enhanced mechanical properties
Gas Nitriding
In gas nitriding the donor is a nitrogen rich gas, usually ammonia (NH3), which is why it is sometimes known as ammonia nitriding. When ammonia comes into contact with the heated work piece it dissociates into nitrogen and hydrogen. The nitrogen then diffuses onto the surface of the material creating a nitride layer.
The process can be accurately controlled. The thickness and phase constitution of the resulting nitriding layers can be selected and the process optimised for the particular properties required.
Advantages of Gas Nitriding Over the Other Variants
- Precise control of chemical potential of nitrogen in the nitriding atmosphere by controlling gas flow rate of nitrogen and oxygen.
- All round nitriding effect.
- Control of the atmosphere for the optimum nitriding results can be closely controlled.
- Relatively low equipment cost - especially compared with plasma.
- Wear resistance: created by a diffused hard surface layer.
- Negligible dimensional changes.
- Improved fatigue properties: the process induces compressive stress to improve fatigue strength.
- Improved corrosion resistance.
- No reduction in the core hardness of the base metal.
- Completed on near finished components requiring minimal (or zero) operations following the process.
- The “white layer” produced by the process can be controlled.
- Can be applied to 'local' areas of any geometry .
Characteristics of the Process
- Low temperature: 495°C to 530°C.
- Flexibly applied - process duration modified according to the specification of the required final component properties.
- Environmentally friendly compared to serious alternatives (e.g. chrome plating).
- Clean for the component - e.g. leaving no heavy surface contaminant or residue.
- Suitable for various steels containing one or more of the following elements, including molybdenum, chromium, aluminium, titanium, vanadium.
Typical Applications:
- Gears,
- Crankshafts,
- Camshafts,
- Cam followers,
- Valve parts,
- Extruder screws,
- Die-casting tools,
- Forging dies,
- Extrusion dies,
- Firearm components,
- Injectors and plastic-mold tools.
Photographs taken prior refurbishment. Our refurbishment service is not available on all machines.
Machines & equipment for sale
- Surface Treatment
- Cleaning & Degreasing
- Polishing & Belt Linishing
- Mass Finishing
- Ovens & Furnaces
- Process Cooling
- Shot Blasting
- Dust & Fume Extraction
- Air Compressors
- Rectifiers & Transformers
- Miscellaneous
- Latest Stock
- Special Offers
- Direct From Site Clearances
- Auctions
- Brand New Machines
- Available Immediately
- Sell Your Machine
Machine Alert
Get the latest machines emailed directly to you as they become available to buy online. Sign Up Now