Kerry ( Guyson International ) Microclean 525/5A Five Stage Ultrasonic Cleaning Machine
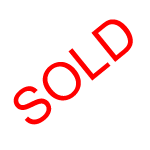
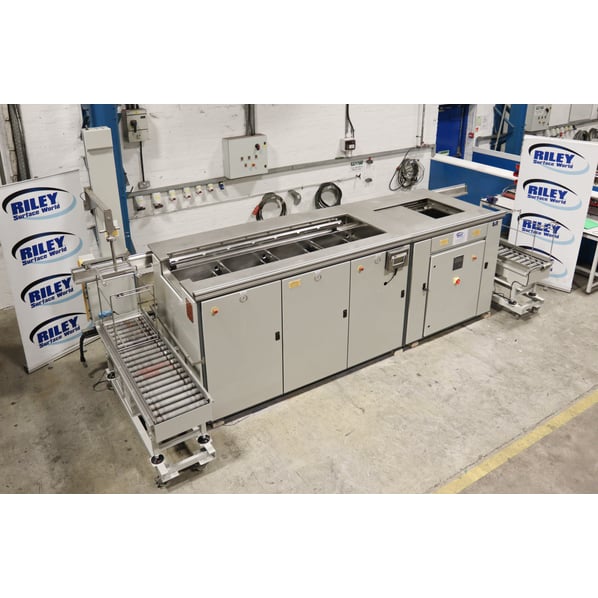
- Stock No
- DD1526
- Manufacturer
- Kerry ( Guyson International )
- Model
- Microclean MF525/5A
- Year of Manufacture
- 2002
- Serial
- CO 61576
- Condition
- From a working environment, Good Condition
- Work Envelope (WxDxH mm) [?]
- 415 x 525 x 350mm
- Process Stages
- 5
- Other Info
- Autotrans Mk4 robotic handler included
- Location
- Our Central Warehouse, Aldridge, UK
- Weight (kgs)
- TBC
- External Dimensions (WxDxH mm) [?]
- Footprint dimensions 5000 x 2625 x 2530
- Delivery Your delivery options
Description
Guyson's Kerry Microclean 5-stage ultrasonic aqueous cleaning system
Stage & Features
- Heated ultrasonic pre-clean.
- Heated ultrasonic with clean rinse.
- Rinse.
- Twin warm air dry
Suits a wide range of cleaning needs in aerospace, engineering, electronics and other sectors.
Closed loop high purity deionised water rinsing provides organic and ionic cleanliness superior to MIL standard.
The Microclean 525/A features include under surface jets and weir overflow to all wet stages.
Additional optional extras fitted.
- Pre-clean 2000 Watt high power ultrasonic module with for heavy duty cleaning
- UV steralisation unit on closed loop DI system
- Vertical basket agitation beam to all wet stages
- Hand pumped wash down brush fixture
- Stage 1,2 and 4 pumped filtration system
- Double capacity hot air drying for increased throughput
- Powered in-feed and out-fall conveyors with basket detection system.
Guyson’s Kerry Microclean 525 is a five-stage ultrasonic cleaning system for use with aqueous chemistries:
Stage 1 - Ultrasonic Pre-Cleaning with heating, spray under immersion, filtration, and optional vertical agitation
Stage 2 - Ultrasonic Cleaning with heating, spray under immersion, filtration, and optional vertical agitation
Stage 3 - Cascade Deionised Water Rinse with spray under immersion, optional vertical agitation
Stage 4 - Final Deionised Water Rinse with spray under immersion, heating and filtration, optional vertical agitation
Stage 5 - Twin Recirculating Warm Air Dry with economy timer; double capacity
The PLC-based electrical control system has a touch screen LCD panel showing actual and set point temperatures, pre-set cycle times, and any faults. An audible signal indicates completion of cycle.
Microclean systems may be operated manually or with the fully automatic Autotrans Mk4 robotic handling system, when the PLC based control system interfaces with the Autotrans to provide fully automatic operation
Technical process specification
Stages One and Two - Ultrasonic Clean
Internal dimensions 415 x 525 x 350mm deep.
The ultrasonic cleaning tank is fabricated in AISI 316 stainless steel and incorporates the following features:
KST submersible ultrasonic transducer positioned to base of tank, radiating face hard chrome plated.
Pulsatron Series 500/4 generators with frequency sweep and automatic tuning, operating frequency 38 kHz ±10%.
Drain overflow and fill pipework with associated valves and protective level control switches.
Electric heating with electronic temperature control and digital indication.
Pumping and filtration system, to include stainless steel pump, pre-filter and 20 inch replacement cartridge type filter element rated 10 micron.
Stage Three - Mains Water Rinse
Internal dimensions 415 x 525 x 350mm deep.
The rinse tank is fabricated in AISI 316 stainless steel and incorporates the following features:
Under immersion sparge pipes connected to water inlet pipework with economy valve.
Drain overflow and fill pipework with associated control valves.
Stage Four - DI Water Rinse
Internal dimensions 415 x 525 x 350mm deep.
The water rinse tank is fabricated in AISI 316 stainless steel and incorporates the following features:
Pumping and filtration system, to include recirculation pump, pre-filter and 20 inch replaceable cartridge type filter rated 1O micron. To allow closed loop recirculation through externally mounted HCC1O activated carbon and HDC1O mixed bed resin cylinders.
Electric heating with electronic temperature control and digital indication. Drain, overflow and fill pipework with associated control valves.
Stage Five - Hot Air Dry
Internal dimensions 830 x 525 x 350mm deep.
The drying chamber is fabricated in AISI 316 stainless steel and incorporates the following features:
Double basket capacity.
Sliding stainless steel lids with automatic open/close operation to interface with Autotrans 1/0 controls.
Electric heating elements positioned within the air outlet manifold and including protective temperature control.
Full width air inlets to two side walls of chamber, air outlets in base and connected to recirculation-blower.
Adjustable air exhaust to prevent moisture saturation. Digital temperature control and indication.
Air Extraction
Stages 1, 2 and 4 incorporate air extraction manifolds which are designed to remove water vapours. All extraction ducting terminates at the rear of plant and is arranged for connection to client's fan and external ducting services.
Vertical Agitation
All wet stages are provided with vertical agitation of the work baskets providing 30 x 50mm strokes per minute.
General Description
The five tank system including all ancillary equipment is mounted in a fully panelled floor standing box section framework. All panels are finished in light grey and are hinged or removable to allow access to all services, stainless steel top surround with lift off lids to wet stages and automatic sliding lids to Stage 5.
Microprocessor Control
The microprocessor electrical control system incorporates a membrane type panel with tactile control buttons and LCD diagnostic panel.
All control switches include LED function indication .
LCD diagnostic panel indicates actual and set point temperatures, fault display and pre-set cycle times with audible cycle complete signal.
MF525/5 footprint dimensions 3800 x 1000 x 1120 mm high.
Overall dimensions including Autotrans automation and load/unload stations 4800 x 1450 x 2800 mm high.
Autotrans MK4 Automation
Designed for fitment to Microclean MF 525/5 system and to include 4800mm horizontal transfer beam.
Mechanical
The transporter head includes linear guide rails and toothed belt drive on vertical carriage with stainless steel pick-up arm mounted to a precision ground steel support rail at low level to the rear of the MF 525/5, the rail is extended to both ends to allow for load/unload.
Both the horizontal and vertical motors (type HD92C4-64T) incorporate electronic torque limiting for system and operator protection, direct reading servo motors provide maximum positional accuracy with automatic positional checking.
Maximum motor speeds are 17m/min vertical, 30m/min horizontal with adjustable ramp rates.
For fully automatic operation including automatic load/unload of the work baskets the fitment of basket 'present' and 'unload' switches are included in the gravity load/unload conveyors (Two 2000 x 600 x 600mm to be positioned at 90 °to the front of the MF525/5) .
Maximum load capacity will be 30 kg and the lift/lower mechanism incorporates basket pick-up carrier fabricated in stainless steel with V block type location points.
Programming
Digital control system reduces wire complexity, ensures signal integrity and allows control functions to be modularised.
Touch sensitive programming key board with LCD sixteen line programming function and prompt display.
Program storage and security is provided by a smartcard
Password protection to prevent unauthorised program interference.
Standard specification allows sixteen programmable 1/0 functions and sixteen flags. The flags can be used for basket position recognition and process timing.
Full edit facilities including position, dwell times and function controls.
Infinitely variable programmable motor speed control
True servo motors with built-in positional encoder ensures positional accuracy to +/- 1mm.
Over travel protection and automatic datumming upon machine installation. RS 232 Interface
Intelligent basket processing allows simultaneous management of varying load types and application of appropriate processing parameters (immersion times, sonics program etc).
DI Water Treatment System
Quantity 2 - HDC10 and quantity 2, HCC10 mixed bed resin and activated carbon cylinders (allows quantity one of each cylinder as spare) together with MCD53 temperature compensated conductivity meter and UV steriliser tube.
Plant Services (to be provided by Client)
- Electrical supply 380/415 volts 3 ph and neutral
- Mains water supply and drain
- Extraction fan and ducting
- Factory specification compressed air.
If purchased as a refurb there will be a new PLC fitted and an external contractor will commission the machine on site.
Photographs taken prior refurbishment. Our refurbishment service is not available on all machines.
Machines & equipment for sale
- Surface Treatment
- Cleaning & Degreasing
- Polishing & Belt Linishing
- Mass Finishing
- Ovens & Furnaces
- Process Cooling
- Shot Blasting
- Dust & Fume Extraction
- Air Compressors
- Rectifiers & Transformers
- Miscellaneous
- Latest Stock
- Special Offers
- Direct From Site Clearances
- Auctions
- Brand New Machines
- Available Immediately
- Sell Your Machine
Machine Alert
Get the latest machines emailed directly to you as they become available to buy online. Sign Up Now