Hedinair 250°C Air Circulation Industrial Oven With Explosion Relief Panels
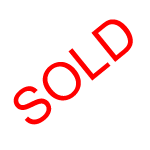
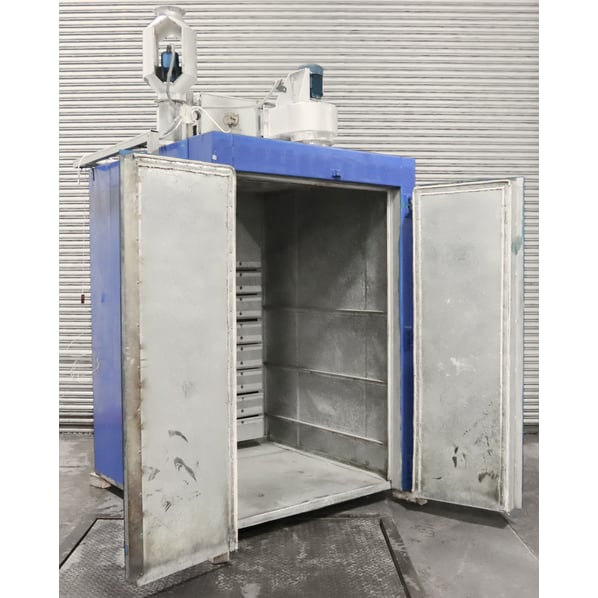
- Stock No
- OD2529
- Manufacturer
- Hedinair
- Model
- Box Oven
- Condition
- Excellent Condition, Seen powered at RSW
- Internal Size (WxDxH mm) [?]
- 1200 x 1200 x 2000
- Max Temp
- 250°C
- Other Info
- Stainless Steel Interior/Forced Cooling
- Location
- Our Central Warehouse, Aldridge, UK
- Weight (kgs)
- 1100 kg
- External Dimensions (WxDxH mm) [?]
- 1860 x 1800 x 3300
- Delivery Your delivery options
Description
A hot air recirculation type of oven, these box ovens are heated by a interior fan for a fan assisted convection process. Constantly recycling the air around the ovens interior to maintain superb temperature consistency.
Intended for all industrial drying, stoving, curing and heating applications from 30˚C to 250˚C. In normal use, these ovens operate at considerably reduced power to simply maintain its internal temperature.
Oven systems offer simple and very accurate digital temperature control, they incorporate electronic over temperature protection, a powered fume exhaust system that can be used for chamber cooling.
Applications
- Paint stoving
- Epoxy/Polyester powder curing
- Lacquer drying
- Hydrosetting
- Moisture removal
- Plastic curing
- Rubber softening
- Metal annealing
- Spring stress relieving
Good Distribution of Heat is Essential for Successful Process
To ensure good performance, all these ovens incorporate medium pressure multi-vane centrifugal fans complete with scroll casings to provide a very positive and well controlled air movement. This is usually several complete air recycles per minute. Large duct work ensures that the high air volume will not disturb the product.
Fume Exhaust System
A powerful and positive, fan assisted, fume exhaust duct system which never relies merely on convection evaporation and it can be adjusted to suit different applications.
Features
- New temperature controller fitted.
- Digital temperature controller.
- Accurate and stable heat control.
- Galvanised steel construction.
- High density mineral wool insulation.
- Fully insulated heater chambers and fans.
- Electronic over temperature protection device.
- External mounted fabricated steel doors
Dimensions : 1860mm x 1800mm x 3300mm
Former Standard AerospaceThese well-maintained machines have come straight from an aircraft engine overhaul facility in the UK. Operated by a global aviation group Standard Aerospace this machinery is well maintained, high-quality and available now from stock out of our warehouse.
|
Purpose of Airflow in Ovens
A popular feature among our range of industrial and laboratory ovens, air circulation is essential for many heat treatments and processes, but it isn’t necessary for all. Seen most typically in high precision ovens for improved temperature accuracy, installing an air circulation system in an oven will distribute the heated air around the oven for a tighter temperature uniformity inside the chamber.
Common Heat Treatments That Use Industrial Ovens & Furnaces
Heat treatment is a controlled process of heating and cooling materials in order to improve its properties, performance, and strength typically made up of three main steps. Firstly heating the metal to a specific temperature, soaking or maintaining the specific temperature for a certain amount of time, and cooling to a suitable rate following prescribed methods.
There are seven main techniques used for the heat treatment of materials, and all affect material in different way. These techniques are:
- Normalising
- Annealing
- Tempering
- Hardening
- Ageing
- Stress Relieving
- Carburisation
Control Features of Your Industrial Oven/Furnace
Many of today's oven/furnace controllers feature multiple screens and options for the operator to adjust to their process, so understanding each of these controls could make the difference in in perfecting your heat process.
The most important features frequently seen on a control panel include:
- On/Off Microprocessor-Based Controller – An on & off heating system to maintain the set temperature.
- PID (Proportional Integral Derivative) Controller – An advanced heat output system to maintain a tight temperature uniformity.
- Digital Process Timer – A timer to set the time length of the process.
- Data Logger – Record the history of previous processes.
- Single Setpoint Controllers – Control the rate of temperature increase & decrease inside the oven chamber.
For more information on each of these features and more, check out our article Essential Features of Industrial Ovens.
Photographs taken prior refurbishment. Our refurbishment service is not available on all machines.
Machines & equipment for sale
- Surface Treatment
- Cleaning & Degreasing
- Polishing & Belt Linishing
- Mass Finishing
- Ovens & Furnaces
- Process Cooling
- Shot Blasting
- Dust & Fume Extraction
- Air Compressors
- Rectifiers & Transformers
- Miscellaneous
- Latest Stock
- Special Offers
- Direct From Site Clearances
- Auctions
- Brand New Machines
- Available Immediately
- Sell Your Machine
Machine Alert
Get the latest machines emailed directly to you as they become available to buy online. Sign Up Now