Carbolite HRT 7/45 750°C Laboratory Bench Top Oven
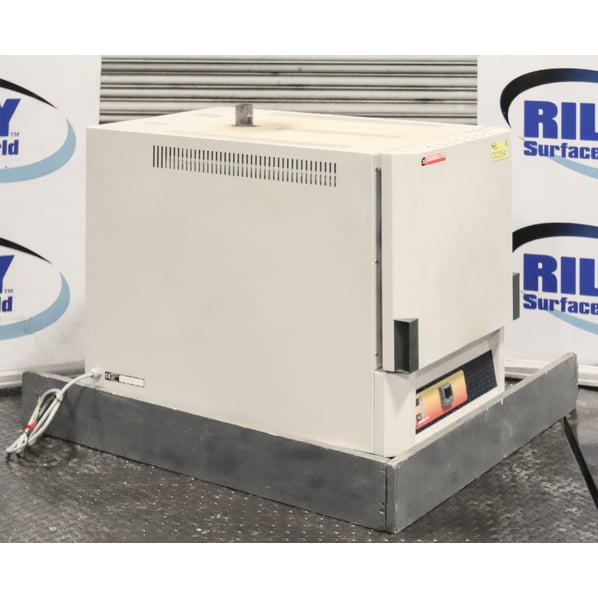
- Stock No
- OD2554
- Manufacturer
- Carbolite
- Model
- HRF 7/45
- Year of Manufacture
- 2011
- Serial
- 21-101342
- Condition
- Excellent Condition, Current Model, Seen powered at RSW
- Internal Size (WxDxH mm) [?]
- 260 x 560 x 290
- Max Temp
- 750°C
- Other Info
- 240Volt Single Phase, 6kW
- Location
- Our Central Warehouse, Aldridge, UK
- Weight (kgs)
- 110
- External Dimensions (WxDxH mm) [?]
- 600 x 1030 x 740
- Delivery Your delivery options
Description
The 750°C HRF air recirculation oven is equipped with powerful fan and horizontal air-guides these models are intended to provide rapid heating with high thermal transfer to the chamber contents and high uniformity within the chamber.
These designs frequently form the base from which custom designed chambers with non-standard sizes or control configurations are made. HRF ovens are often supplied with modifications to enable heat treatment within AMS 2750E Nadcap compliant production environments.
Standard Features
- 750°C maximum operating temperature.
- 45 litre chamber volume.
- Wire elements located in both sides of the chamber.
- Stainless steel liner.
- Combination of low thermal mass and refractory board insulation.
- Carbolite Gero 301 controller, with single ramp to set-point & process timer
Ventilation
If the furnace is to be used for heating materials which produce smoke or fumes, the chimney must be correctly fitted and unobstructed. Otherwise, soot will accumulate in the chamber and between the layers of insulation, causing an electrical breakdown of the heating elements. Furnaces used for this kind of application must be heated regularly up to maximum temperature and held for one hour to burn away the soot.
Corrosive Materials
Materials such as case hardening compounds and other reactive salts readily penetrate the ceramic lining of the furnace chamber and attack the wire elements, causing premature failure. When such materials are being used, the furnace must be protected by a hearth plate or tray, preferably made from material such as inconel.
Non-metallic hearth plates reduce the heat transmission from the bottom of the furnace, and increase the element temperature in this area. This may result in premature element failure, particularly if the furnace is working near to maximum temperature. Under these circumstances, it is recommend that the temperature be raised slowly over the last 300°C, allowing approximately 10 minutes soak at 100°C intervals.
Technical Data
- Model: 7/45
- Maximum temperature: 750°c
- Maximum power rating: 6kW
- Chamber: 265mm x 560mm x 295mm
- Eurotherm controller 3216
Control Features of Your Industrial Oven/Furnace
Many of today's oven/furnace controllers feature multiple screens and options for the operator to adjust to their process, so understanding each of these controls could make the difference in in perfecting your heat process.
The most important features frequently seen on a control panel include:
- On/Off Microprocessor-Based Controller – An on & off heating system to maintain the set temperature.
- PID (Proportional Integral Derivative) Controller – An advanced heat output system to maintain a tight temperature uniformity.
- Digital Process Timer – A timer to set the time length of the process.
- Data Logger – Record the history of previous processes.
- Single Setpoint Controllers – Control the rate of temperature increase & decrease inside the oven chamber.
For more information on each of these features and more, check out our article Essential Features of Industrial Ovens.
Common Heat Treatments That Use Industrial Ovens & Furnaces
Heat treatment is a controlled process of heating and cooling materials in order to improve its properties, performance, and strength typically made up of three main steps. Firstly heating the metal to a specific temperature, soaking or maintaining the specific temperature for a certain amount of time, and cooling to a suitable rate following prescribed methods.
There are seven main techniques used for the heat treatment of materials, and all affect material in different way. These techniques are:
- Normalising
- Annealing
- Tempering
- Hardening
- Ageing
- Stress Relieving
- Carburisation
Print / Download Carbolite HRT 7/45 750°C Laboratory Bench Top Oven Datasheet
Additional files
Photographs taken prior refurbishment. Our refurbishment service is not available on all machines.
Machines & equipment for sale
- Surface Treatment
- Cleaning & Degreasing
- Polishing & Belt Linishing
- Mass Finishing
- Ovens & Furnaces
- Process Cooling
- Shot Blasting
- Dust & Fume Extraction
- Air Compressors
- Rectifiers & Transformers
- Miscellaneous
- Latest Stock
- Special Offers
- Direct From Site Clearances
- Auctions
- Brand New Machines
- Available Immediately
- Sell Your Machine
Machine Alert
Get the latest machines emailed directly to you as they become available to buy online. Sign Up Now