Ryeford Engineering Stainless Steel Ardrox 311 Oiling Line with Pall Dewatering Filter System & Solution Cooling.
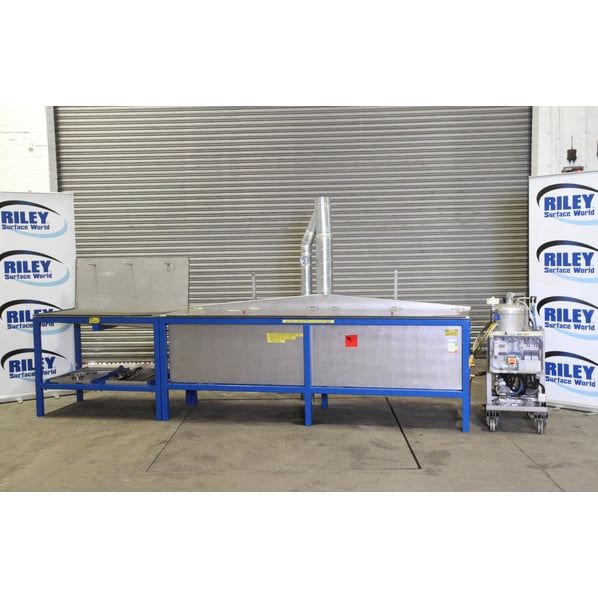
- Stock No
- DA1413
- Manufacturer
- Ryeford Engineering
- Model
- Pall Fluid Conditioning Purifier HNP006
- Year of Manufacture
- 2006
- Serial
- PHNPM0057
- Condition
- Seen working by RSW, Excellent Condition
- Work Envelope (WxDxH mm) [?]
- Baskets 510 x 510 x 250 with 3 mesh
- Process Stages
- Oiling, De-watering and Cooling
- Other Info
- Bunded, lip extraction, drain station
- Location
- Our Central Warehouse, Aldridge, UK
- Weight (kgs)
- 350 (Tank)
- External Dimensions (WxDxH mm) [?]
- 4600 x 1400 x 2000
- Delivery Your delivery options
Description
Ardox 311 Oiling Line Including Stainless Cleaning Tank and Pall Fluid Conditioning and De-watering Purifier.
Quality freestanding stainless steel single stage oiling / cleaning process tank line. Internal tank size 2480 x 630 x 570mm.
Basket type degreasing and cleaning tank with:
- Heat exchanger.
- Distribution pump.
- Transformer.
- Spill tray bund.
- Exhaust lip extraction to atmosphere.
- 2 off manually operated lids - 2550mm x 640mm x 570 mm dimensions.
- Quantity of Baskets 510mm x 510mm x 250mm with 3mm mesh.
Additional to the cleaning tank:
- Ardrox 311 Draining Station.
- Pre Packing, Post Ardrox Work Station.
- Process Solution Cooling plant.
- Additional Work Station.
Pall Fluid Conditioning Purifier
HSP Portable Oil Purifier - The Pall Hydraulic Spinning Disc Purifier (HSP) has been developed as a conditioner for hydraulic and lubrication oils. It removes water, dirt and air and is economical, compact, mobile and easy to use.
Model: HNP006
Machine ref: HNP006F5APHC
Serial no: PHNPM0057
Description of Operation
General
The HNP portable oil fluid conditioning purifier conditions hydraulic and lubrication fluids by removing water, particulate contamination and gases.
It is designed for a power supply as detailed on the unit nameplate, which is transformed to 24V DC for the control circuit.
The HNP006 series is a fluid purification system designed to remove the following contamination:
- Water- 100% of free water and in excess of 80% of dissolved water.
- Gases - 100% of free and entrained gases and in excess of 80% of dissolved gases.
- Dirt - including silt and other solids or particulate contaminants.
Principles of Operation
The contaminated oil is passed through the purifier vessel via the nozzle. Fluid sprays outward from the nozzle and falls under gravity to the bottom of the vessel, air and water being removed through the top of the vessel by the airflow.
Air is drawn out of the top of the vessel by the vacuum pump. In flowing through the vessel, the contaminated oil presents a large and constantly changing surface area to the dry airflow. The dry air passes over the wet oil and moisture is transferred from the oil into the airflow.
The dry air is obtained by producing a vacuum inside the purifier vessel When ambient air is drawn into the side of the vessel through the vacuum adjustment valve, it expands to approximately three times its former volume (based upon factory vacuum setting of -0.7 bar g / 20.7 in Hg). The amount of water in grams in the air does not change. With the volume having been increased by 3 times, it now has a much lower percentage of water; the air has effectively been dried. The vessel vacuum also expands any dissolved gas within the oil. The gases and water vapour are then discharged to atmosphere via the vacuum pump.
Design Operating Conditions
- Fluid - to be compatible with seal material.
- Inlet pressure: bar g / psi 0 to +10/0 to 145.
- System back pressure: bar g / psi 0 +2/ 29 maximum.
- Outlet relief valve: barg / psi 10/145.
- Service temperature: °C/°F 10 to 70/50 to 158.
- Maximum fluid viscosity: cSt / SUS 700/3300.
- Minimum fluid viscosity: cSt/SUS 12/68.
- Fluid system.
- Circulating rate.
- 50Hz units - 10/2.6 (l/min/).
- Batch volume - 3.0/0.78 (1/ US Gall).
Materials of Construction
- Base frame - stainless steel.
- Vessel - stainless steel.
- Control box - polycarbonate.
- Relief valve - brass.
- Threaded fittings, fasteners - corrosion protected carbon steel.
- Hoses - chlorinated polyethene.
- Seals - fluorocarbon.
Motor and Drive System
- Type- direct online.
- Power supply - 13 amps.
- Control voltage - V DC 24.
- Total motor power - 50Hz units kW/HP - 0.67/0.9.
- Motor rating - vacuum pump 50Hz units kW – 0.3.
- Fluid pump - 0.37 kw.
- Power supply fuse rating - to suit full load current shown on unit nameplate.
- Motor circuit breaker settings - to suit full load current shown on unit nameplate.
Aerospace Packing Area Cleaning, Oiling and Bag Sealing CellThis machine was originally part of a cell that worked on the following basis.
Stage 1: Kerosene (Exxsol D80) Spray Wash [DA1414 - Vixen Tristar]Components are placed on the Vixen wash belt conveyor to be spray washed with Kerosene (exxsol D80), the speed of the conveyor is adjustable to achieve the required cleaning result an optical sensor at the end of the conveyor will stop the conveyor when a part is detected making unattended operation possible.
Stage 2: White Spirit DipThe components are removed from the Vixen spray wash and placed in a basket, the basket is placed in the white spirit tank and manually agitated up and down to remove the kerosene. The basket is the paced on the side draining board and left for a short period of time for any excess white sprit to drain off back into the tank.
Stage 3: DryingThe components are removed from the now drained basket and placed in the drying oven on a stainless steel tray, the oven temperature is set to 110 degrees centigrade the time in the oven is dependent on the shape complexity of the component, complex shaped components are left in the oven for 2 hours simple shaped components for 1 hour.
Stage 4: Oil Dip [DA1413 Heated Cleaning Tank]At the end of the drying time the components are removed from the oven and either placed in a basket or on a jig and completely submersed in the oil tank containing Ardrox 311. Ardrox 311 is Hygroscopic i.e. it absorbs moisture from the air, it is for this reason the oil tank is equipped with a Pall moisture sensor and Pall Purifier. The pall purifier pumps a measured amount of oil out of the tank into a chamber which is under vacuum the oil is spread thinly on a plate and the moisture evaporates back to the atmosphere the now ‘dry’ oil is then pumped back to the tank and the process is repeated for the next measured amount, this can continue until the desired moisture level is achieved. The tank is also equipped with a circulating pump and oil cooler, with hot parts being submerged into the Ardrox 311 the temperature of the oil gradually rises and should not be used above 30 degrees Celsius the, oil cooler can be set to operate at a temperature that will maintain the oil tank temperature below 30 degrees Celsius.
Stage 5: Draining [DA1413 Heated Cleaning Tank]When the components are cool enough to handle they are removed from the oil tank and placed on a draining board next to the oil tank to allow any excess oil to drain off and pass back to the oil tank
Stage 6: IdentificationOnce the excess oil is drained off the unique component identifier is found on the component and written on the packing bag. The component is placed inside the bag.
Stage 7: Bag SealingThe now bagged component is placed on the Radyne RF bag sealer. The Radyne RF bag sealer utilises radio frequencies to heat fiberglass tape covered blades to seal the bag. The open end of the bag is at first not complete sealed enough room is left to insert the suction pipe from the vacuum pump to be inserted into the bag. The vacuum pump is operated by a foot switch keeping the operators hands free to manipulate the bag and component, the air is sucked out of the bag and the final seal is made completely sealing the bag. |
Additional files
Photographs taken prior refurbishment. Our refurbishment service is not available on all machines.
Machines & equipment for sale
- Surface Treatment
- Cleaning & Degreasing
- Polishing & Belt Linishing
- Mass Finishing
- Ovens & Furnaces
- Process Cooling
- Shot Blasting
- Dust & Fume Extraction
- Air Compressors
- Rectifiers & Transformers
- Miscellaneous
- Latest Stock
- Special Offers
- Direct From Site Clearances
- Auctions
- Brand New Machines
- Available Immediately
- Sell Your Machine
Machine Alert
Get the latest machines emailed directly to you as they become available to buy online. Sign Up Now