Essential Features of Industrial Ovens
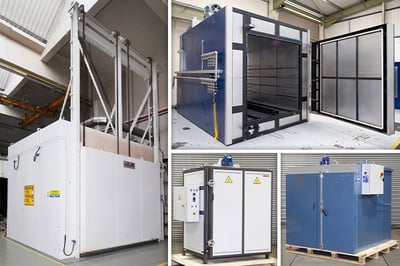
Are you looking to buy an industrial oven? Are you unsure what features you need for your heat process?
This is a guide to explain and break down those core features you need to consider when choosing and using an industrial oven, continue reading to find out what they are and how they could benefit your process.
Controls
Most industrial ovens now use digital controllers but are often accompanied by analogue controls such as emergency stop buttons or dial based over temperature protection.
Controllers can be all-in-one or a device for each feature, so it is important to understand the role each controller feature plays.
On/Off Microprocessor-Based Controller
One of the simplest digital temperature controllers frequently installed in an industrial oven, the on/off control system is self-explanatory when describing how it maintains the temperature inside the oven. The ‘on’ means when the temperature is below the set temperature, activating the heating system to increase the internal temperature. The ‘off’ is when the temperature has exceeded the set temperature, and the heating system is switched off to reduce the temperature. This is a simple, effective heating control system suitable for many processes.
PID (Proportional Integral Derivative) Controller
The more advanced digital temperature controller for more precision ovens, a PID controller manages the heat output more carefully than a simple on/off to reduce temperature variation during a heat process (temperature uniformity). By using short bursts of heat or a proportional amount of power, a PID controller can maintain an accurate and stable temperature setpoint, determining the percentage of heat required in advance for the process.
Temperature Sensors
The essential system for how the oven gathers its information for operation is temperature sensor probes fitted in the internal wall of the oven to detect the temperature inside the operating chamber. The number of temperature sensor probes varies depending on the precision requirements of the oven; the more sensors inside the oven provide a more accurate reading across the oven chamber.
The most common form of temperature sensor is of course the thermocouple. These are formed from two metals with different electrical conductivity which produce a measurable voltage when heated. Accuracy varies with quality and cost so thermocouples need to be matched to the temperature range and precision required..
Digital Process Timer
A digital process timer can be a separate control feature or (more likely) part of a multi-feature digital controller. Controlling one of the most important but straightforward variables for a process, they can set the time length of a process or start a process at a particular time.
Data Logger
A convenient feature in an industrial oven to record the history of previous processes, data loggers can be beneficial for:
- Replicating previous processes.
- Investigating processes from past component batches.
- Keeping track of experimental processes for R&D purposes.
Data Loggers are essential in some industries where component traceability is required. Data can be collected by printing onto paper charts, stored and downloaded onto USB drives for computer analysis or even collected remotely by connecting to a computer network.
Single Setpoint Controllers - Programmable Ramp/Soak Controllers
A more advanced feature essential for higher precision industrial ovens, setpoint controllers manage the rate the temperature increases and decreases inside the oven chamber. Multiple set points can be useful during the heat treatment to maintain the chamber at lower temperatures before reaching the target temperature or to control the rate of temperature changes so as not to cause heat stress to a component. An example is the requirement of controlled cooling when sterilising glassware to prevent potential cracking.
Heating Components
Electric/Gas Heated
As the most common heating options for industrial ovens, electric & gas heating methods are both quick when it comes to heating the oven chamber to the set temperature, along with their own individual benefits. Generally, gas powered ovens cost more initially but are cheaper to run and known for maintaining temperature well. At the same time, electric ovens cost less for the machinery and excel for their precision. Electric ovens are also ideal for processes that involve combustible substances and metals like aluminium that can discolour from gas.
Airflow System
How the heat is distributed inside the oven is all down to the airflow pattern inside the chamber. Several components can be combined to manage airflow such as an exhaust chimney, extraction fans, internal circulation fans or an air filtration system. In a gravity convection oven, the ‘natural’ airflow may be all that is used, while in a forced air circulation oven, it may require the complete system for constant airflow.
Furthermore, the airflow pattern inside the oven is built to direct air in a specific pattern, which is vital for the type of components and batch volumes the industrial oven would be used for. To learn more about the importance of airflow and the relevance of its direction on your components, check out Purpose of Air Flow During Heat Treatment.
Core Construction
Powder Coated Steel Exterior
An exterior coating commonly used for its professional finish across many industries, a powder coating finish offers more benefits than just an appealing aesthetic. Able to offer additional protection, durability and corrosion resistance against surface damage, it is standard practice for ovens constructed with mild steel to be powder coated. The coating provides some corrosion resistance properties mild steel doesn’t have compared to more expensive oven construction materials such as stainless steel.
Stainless Steel Chamber
A frequent material for industrial ovens, stainless steel is highly desirable for its heat resistance, high tensile strength, corrosion resistance and low maintenance properties when it comes to ovens. A strong & resistant material perfect for withstanding processes of heavy weight, high temperatures or explosive risks. Used either for the interior chamber or interior & exterior, it’s the go-to material for high specification & temperature (up to 750°C) ovens.
Oven Insulation & Wall Panels
Located between the internal chamber and external wall, the insulation inside these panels is essential to retain heat for an efficient design. Reducing running costs and preventing risk to the user by keeping the external surface cool. The panels are padded with insulating materials such as thermal insulation boards and blankets made of various fibres like rock wool.
Loading Door
Vertical or horizontal? One door or two doors? Manual or powered? As simple as this feature is, the loading door is critical when factoring in the floorspace surrounding the oven, the size of the components, the processes it will be used for, and the equipment required for loading.
Inside premises with limited floor space or low ceilings, space is required to open the door and load the components with a trolley, forklift or manually (depending on the component size or batch volume). When trolleys and forklifts transport components, space is needed to load the parts and put the trolley into the oven. Then for processes that demand the components to still be hot when they come out, the loading door needs to be an option that offers protection to the operator when opening from the heat.
Oven Floor
A feature that is critically important when specifically considering where an industrial oven will be placed is the base of the oven, which has surprisingly many options.
A typical base would be insulated (like the wall panels) for improved efficiency and heat protection for the floor. Barrel warming ovens that heat large volumes of substances frequently have no floor as the temperatures required are too low to damage a typical concrete factory floor and don’t require the most accuracy. A basic flat floor made out of a steel sheet could be installed to act as the barrier between the floor and components. While alternatively, ventilated floors would be seen in ovens aiming for maximum vertical airflow or when the heating elements are located in the base.
Safety Features
Explosion Relief
In any process that features an oxygenated space with combustible materials, explosion relief should be considered for controlling and handling any explosions that could occur inside the oven chamber. The features to withstand this are all built into the design of the oven, including explosion relief panels within the walls to relieve any explosions of the pressure release and durable explosion-proof door locks to withstand it.
Positive Force Ventilation
Not to be mistaken with the fan in the airflow system that circulates air internally, this separate fan would be located near the exhaust or chimney of the oven, forcing air out of the oven. To maintain the airflow and fume control cycle, the ventilation system works with the recirculation system for optimum temperature precision while regulating any fumes from potentially combusting or contaminating/depreciating the quality of the components during the heat process.
Airflow Safety Switch
For industrial ovens with forced airflow, this switch is one of the steps of starting a process; without it, the process won’t start.
Purge Timer
Another pre-process feature, this required step focuses on removing idle vapours, fumes and gases, which could present risk and contamination to the process. The gases are purged from the oven chamber by activating the airflow and exhaust fans before the process.
Over Temperature Protection (OTP)
The over-temperature protection device is the first protection against the oven from overheating above the set temperature or max temperature of the oven. Set at a temperature above the process requirements or maximum operating temperature, when the heat inside the chamber reaches that temperature, it will trip the oven temperature protection and shut down the process. Over temperature protection is essential for safety and commercially to avoid damaging components.
Oven Accessories
A few more common features that vary from oven to oven are these accessories, which play key roles in how the operators use these ovens on a per-process basis.
- Loading Trolley– A structure on wheels built to transport components to and from an oven and go in the oven during heat treatment as a shelving alternative.
- Railings– Ceiling tracks to allow components to be hung in the oven for optimum airflow reach.
- Tracks– Pathway in the base of the oven chamber for a loading trolley.
- Shelving– Ridges and slots in the interior walls of the chamber for shelves (fixed or adjustable) to allow for larger batch volumes.
- Legs– Typically reflective of a factory's pre-existing production setup or to manage heat by lifting the oven from the floor.
Deciding on the Industrial Oven for You
Summarising the variety of common features we see in industrial ovens; please note this isn’t all of them. With further specialist ovens such as vacuum ovens and conveyor ovens, including individual features of their own, it is where our expertise in industrial ovens can help you.
If you’re looking for an industrial oven with precision features or need to be of a high industry specification, check out our full range or call our sales team at +44(0)1922 45 8000 to find the perfect oven for you.
JLS (Redditch) Ltd 300°C Precipitation Hardening & Ageing Oven - AMS2750D
JLS precipitation hardening & ageing, forced convection oven built to AMS2750D & Nadcap class 2 (± 5°C) standard, previously used for the heat treatment of aluminium aerospace components and last calibrated November 2024.
- Stock No
- AEF300
- Category
- Industrial Ovens
- Model
- JLS (Redditch) Ltd Precipitation Hardening & Ageing Oven
- Year of Manufacture
- 2008
- Internal Size (WxDxH mm) [?]
- 1200 x 2500 x 1200
- Max Temp
- 300°C
- Other Info
- Calibrated November 2024 ± 5°C @ 200°C
- Condition
- Seen working by RSW, Excellent Condition
- Location
- Bolton, Greater Manchester, UK
- Price [?]
- Please call on +44 (0) 1922 45 8000
- Part of a Direct Site Clearance
- Aeroforma - Aerospace Quality Machinery
SNOL 350°C Industrial Oven Range
350°C general purpose batch ovens, ideal for a vast range of low temperature thermal processes such as drying, curing and pre-heating.
- Stock No
- NEW070
- Category
- Industrial Ovens
- Model
- SNOL
- Internal Size (WxDxH mm) [?]
- Various
- Max Temp
- 350°C
- Condition
- Brand New
- Availability:
- Available subject to build time
- Price [?]
- Please call on +44 (0) 1922 45 8000
SNOL 650°C High Temperature Oven Range
General purpose high temperature, industrial, batch ovens which set the standard for a wide range of industrial processing applications
- Stock No
- NEW071
- Category
- Industrial Ovens
- Model
- SNOL
- Internal Size (WxDxH mm) [?]
- Various
- Max Temp
- 650°C
- Condition
- Brand New
- Availability:
- Available subject to build time
- Price [?]
- Please call on +44 (0) 1922 45 8000
SNOL 650°C High Temperature Oven with Powered Door
General purpose high temperature, industrial, batch oven suitable for a wide range of industrial processing applications. Includes a vertical powered door.
- Stock No
- NEW072
- Category
- Industrial Ovens
- Model
- SNOL
- Internal Size (WxDxH mm) [?]
- 600 x 750 x 900
- Max Temp
- 650°C
- Availability:
- Available subject to build time
- Price [?]
- Please call on +44 (0) 1922 45 8000
SNOL Custom Build Furnaces & Ovens
Custom built ovens and furnaces to meet your project requirements and standards.
- Stock No
- NEW079
- Category
- Industrial Ovens
- Model
- SNOL
- Condition
- Brand New
- Availability:
- Available subject to build time
- Price [?]
- Please call on +44 (0) 1922 45 8000
Romer 200°C Industrial Oven Range
200°C general purpose, electric, batch ovens from 3.4m3 upwards. Ideal for a vast range of low temperature thermal processes such as drying, curing and pre-heating.
- Stock No
- NEW080
- Category
- Industrial Ovens
- Model
- Romer
- Internal Size (WxDxH mm) [?]
- Various
- Max Temp
- 200°C
- Other Info
- Touchscreen Control plus iCure Software
- Condition
- Brand New
- Availability:
- Available subject to build time
- Price [?]
- Please call on +44 (0) 1922 45 8000
Romer 200°C Convection Industrial Oven Range
200°C electric, batch ovens from 3.4m3 upwards. Without a fan' these ovens are a very cost effective option or ideal for delicate processes that cannot tolerate air movement.
- Stock No
- NEW081
- Category
- Industrial Ovens
- Model
- Romer
- Internal Size (WxDxH mm) [?]
- Various
- Max Temp
- 200°C
- Other Info
- Radiant heating
- Condition
- Brand New
- Availability:
- Available subject to build time
- Price [?]
- Please call on +44 (0) 1922 45 8000
Romer Essential Electric Oven Range
200°C general purpose, electric, industrial ovens from 3.4m3 upwards. Ideal for a vast range of low temperature thermal processes such as drying, curing and pre-heating. The Essential range is a cost effective solution where temperature recording is not required.
- Stock No
- NEW082
- Category
- Industrial Ovens
- Model
- Romer
- Internal Size (WxDxH mm) [?]
- Various
- Max Temp
- 200°C
- Condition
- Brand New
- Availability:
- Available subject to build time
- Price [?]
- Please call on +44 (0) 1922 45 8000
Romer 300°C Industrial Oven Range
350°C general purpose, electric, batch ovens from 0.9m3 to 8.4m3 in size. Ideal for low to medium temperature thermal processes such as drying, curing and pre-heating.
- Stock No
- NEW083
- Category
- Industrial Ovens
- Model
- Romer
- Year of Manufacture
- Brand New
- Internal Size (WxDxH mm) [?]
- Various
- Max Temp
- 300°C
- Other Info
- Touchscreen Control plus iCure Software
- Condition
- Brand New
- Availability:
- Available subject to build time
- Price [?]
- Please call on +44 (0) 1922 45 8000
Romer 600°C Industrial Oven Range
600°C general purpose, electric, batch ovens from 0.9m3. Ideal for range of medium to high temperature thermal processes. Ideal for tempering, glass annealing, drying, preheating, and stress relieving of various materials.
- Stock No
- NEW084
- Category
- Industrial Ovens
- Model
- Romer
- Year of Manufacture
- Brand New
- Internal Size (WxDxH mm) [?]
- Various
- Max Temp
- 600°C
- Other Info
- Touchscreen Control plus iCure Software
- Condition
- Brand New
- Availability:
- Available subject to build time
- Price [?]
- Please call on +44 (0) 1922 45 8000
Romer Custom Built Industrial Ovens
Romer and RSW are working together to offer custom built ovens manufactured to your requirements and specifications. The perfect solution if you know what you need and cannot get it as a standard oven. High quality build standards and low prices define a very competitive package.
- Stock No
- NEW085
- Category
- Industrial Ovens
- Model
- Romer Various
- Year of Manufacture
- 2023
- Internal Size (WxDxH mm) [?]
- Various
- Other Info
- Custom Ovens For customer requirements.
- Condition
- Brand New, Unused, Current Model
- Availability:
- Available subject to build time
- Price [?]
- Please call on +44 (0) 1922 45 8000
Romer 250°C Industrial Oven Range
250°C general purpose, electric, batch ovens from 3.4m3 upwards. Ideal for a vast range of low temperature thermal processes such as drying, curing and pre-heating.
- Stock No
- NEW086
- Category
- Industrial Ovens
- Model
- Romer
- Year of Manufacture
- Brand New
- Internal Size (WxDxH mm) [?]
- Various
- Max Temp
- 250°C
- Other Info
- Touchscreen Control plus iCure Software
- Condition
- Brand New
- Availability:
- Available subject to build time
- Price [?]
- Please call on +44 (0) 1922 45 8000
Romer 350°C Industrial Oven Range
350°C general purpose, electric, batch ovens from 0.9m3 to 8.4m3 in size. Ideal for low to medium temperature thermal processes such as drying, curing and pre-heating.
- Stock No
- NEW087
- Category
- Industrial Ovens
- Model
- Romer
- Year of Manufacture
- Brand New
- Internal Size (WxDxH mm) [?]
- Various
- Max Temp
- 350°C
- Other Info
- Touchscreen Control plus iCure Software
- Condition
- Brand New
- Availability:
- Available subject to build time
- Price [?]
- Please call on +44 (0) 1922 45 8000
Efco Top Loading Roller Lid Electric Drying and Treatments Oven
Efco Top Loading Well Type Roller Lid Electric Drying and Treatments Oven
- Stock No
- OA2172
- Category
- Industrial Ovens
- Model
- Efco Well Type Drying and Treatments Oven
- Year of Manufacture
- 08.1999
- Internal Size (WxDxH mm) [?]
- 1800 x 1800 x 2000
- Max Temp
- 150°C
- Other Info
- High 36kw rating
- Condition
- Seen working by RSW, Excellent Condition
- Location
- Rolls Royce stores, near Derby, UK
- Availability
- Available for immediate collection
- Sold As Seen Price [?]
- £ Login or Register for price.
Contract Engineering and Trading SDN BHD Fully Stainless Steel Air Circulated Front and Rear Door Box Oven
120°C Stainless Steel constructed through oven. Originally designed for the food / pharmaceutical industry but could be used in many industries.
- Stock No
- OA2229
- Category
- Industrial Ovens
- Model
- Contract Engineering and Trading SDN BHD YOUD2 R6H
- Year of Manufacture
- 2005
- Internal Size (WxDxH mm) [?]
- 835 x 1780 x 1945
- Max Temp
- 120°C
- Other Info
- Front and Rear Through Door Operation
- Condition
- From a working environment, Good Condition
- Refurbished Price [?]
- £ Login or Register for price.
- Sold As Seen Price [?]
- £ Login or Register for price.
Machines & equipment for sale
- Surface Treatment
- Cleaning & Degreasing
- Polishing & Belt Linishing
- Mass Finishing
- Ovens & Furnaces
- Process Cooling
- Shot Blasting
- Dust & Fume Extraction
- Air Compressors
- Rectifiers & Transformers
- Miscellaneous
- Latest Stock
- Special Offers
- Direct From Site Clearances
- Auctions
- Brand New Machines
- Available Immediately
- Sell Your Machine
Machine Alert
Get the latest machines emailed directly to you as they become available to buy online. Sign Up Now