The Ancillary Equipment Guide to Plating Lines
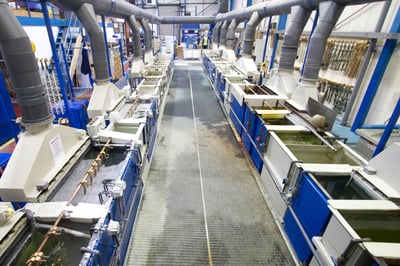
Plating and treatment lines are the most complex machinery on sale at Riley Surface World with a wide range of ancillary equipment available to customise any line. Each feature of a plating line process brings its own range of variations to make the line suitable for specific applications or components; continue reading to find out what ancillary equipment makes up a plating line.
Rectifiers
Many plating lines rely on the conversion of electricity from AC (alternating current) to DC (direct current) for the plating processes such as electroplating, and rectifiers make this electrical transformation happen. By altering the voltage & level of the DC current, the thickness and quality of the plating can be altered. Historically, low-voltage generators were often used to create the DC output for plating, but their high cost and maintenance have resulted in rectifiers becoming the modern-day preference as a more economical alternative.
Tank Heaters
Temperature control is a critical factor for plating, often varying between the specific process solutions being used. Knowing these temperatures and keeping the solutions in the tanks at a consistent temperature range is just another factor that can optimise the plating quality for the final components. These temperatures can range from 30°C for copper plating up to 90°C for electroless nickel.
To achieve the required conditions, heat exchangers & vat heating elements (available in the form of various cylindrical rods to flat panels) are typically built into the design of the plating line, usually installed on the inside of the tanks.
It is worth noting in today's plating lines that these heaters are most commonly electric, having previously been gas or steam. Electric heaters are easier to use with less maintenance. Options to reduce a plant’s carbon footprint are available with heat exchange, recycling and insulation.
Filtration Systems
Maintaining clean plating solutions is essential for achieving high-quality coatings, as impurities and contaminants in the plating bath can impact the final appearance of the component. Often these contaminates cannot be prevented as they are produced by just running the plating line, preventive measures can be taken instead to prevent them from building up with the use of filtration systems.
Able to be carried out in a periodic or continuous manner (depending on the plating solutions being used), the filtration takes place in an adjoining chamber to the main bath of solution with a pump to circulate it through. As the preferred option for reduced contamination levels, continuous filtration systems take place in two of these chambers. The first contains a filter to remove particles of various micron sizes and the second features a carbon filter to remove all the organic contamination such as breakdown products in the solution. For solutions prone to more impurities, the turnover rate of filtering the entire contents of the tank would need to be increased from a more standard 2 to 3 turnovers an hour to 4 to 5 turnovers an hour.
Chemical Dosing Systems
The other system to support the plating solutions during plating is the chemical dosing system. The purpose of this system to maintain the chemical properties of the plating solution, it keeps the solution topped up with the additives and chemicals to maintain those capabilities. This is usually done pro-rata to ampere time or surface area of work processed through the bath.
Consisting of chemical preparation tanks, dosing pumps, and other interconnected components sensors in the form of flow meters communicate with the dosing pump adding various chemicals such as brighteners, wetting agents and pH-buffering chemicals.
Cathode Bars, Racks & Barrels
Used to conduct the negative charge from the rectifier to the components being plated, a cathode bar may not always be in the physical form of a bar, often fitted as saddles fitted to the tank flange. Components can be processed on jigs which are attached to the cathode bar in the plating bath, or on racks & inside barrels which fit onto the cathodic location saddles.
The form of these structures depends on the nature and geometry of the components being plated. For large components, cathode bars are a sturdy structure to typically suspend the parts from; while a rack is best suited for medium components as it is an effective way to process multiple parts at once. Practical for processing large batches of smaller components, the barrel is a popular go-to.
The purpose of these structures is to transport the components through the plating process, tank to tank.
Extraction/Fume Scrubbers
In any process that produces mists & fumes, extraction is a must for the plant to be compliant with the Control of Substances Hazardous to Health Regulations (COSHH). Fumes from the chemical process for plating are a potential hazard to the health of the workforce. As well as a cause of significant corrosion to the fabric of the building and damage other components in process within the facility. Therefore, essential that these fumes are captured and controlled with the use of localised extraction systems that are usually built into the plating line to contain these risks.
Ways plating lines are designed to control mists & fumes include:
- Lip Extraction: Made up of fume capture hoods fitted to the tank flange, they are often fitted at the rear of the tank but can be single or double-sided depending on the width & surface area of the tank. Further connected by ductwork manifolds to an extraction fan and discharge stack to the atmosphere.
- Abatement Systems: To be in line with the various air quality regulations that establish the limit of contaminates discharged into the air, an example of these controlled chemicals can include oxides of nitrogen and nickel. For chemicals that produce emissions of controlled substances, the fumes must be cleaned/neutralised prior to discharge to the atmosphere via an abatement system. These systems take the form of vertical fume scrubbing towers, horizontal mist elimination and filtration systems depending on the application.
- Tank Lids: Adding lids to tanks keeps the fumes and mists over the tank, reducing the volume of air that needs extraction, and therefore power of the extraction system. Lids are most typically powered but can also be manually operated to fit in with a process.
Your Next Plating Line
As this article is an introduction to the ancillary equipment that goes into a functional plating line, feel free to approach us with enquiries you may have about our used plating line opportunities. Having supplied plating plant for over 55 years, Riley Surface World is well experienced and knowledgeable when it comes to plating lines.
If you are interested in one of our plating or are looking for some of the supportive equipment mentioned in the article, contact us at +44(0)1922 45 8000 or throw us an email at [email protected].
Jacquet Weston Engineering Packaged Demineralisation Water Treatment Plant
Manually operated, the de-mineralisation unit produces up to 200 l/h when connected to a 1,000 litre holding tank. At the estimated hourly production of 45 l/h demineralised water the unit will need regenerating every 75-80 hours.
- Stock No
- MA748
- Category
- Electroplating & treatment lines
- Model
- Jacquet Weston Engineering Ion Exchange Plant
- Work Envelope (WxDxH mm) [?]
- Brake / Storage Tank Ø900 x 1500
- Process Stages
- Single Stage
- Other Info
- Producing up to 200 litres/hour
- Condition
- From a working environment, Good Condition
- Sold As Seen Price [?]
- £ Login or Register for price.
Eagle Engineering and Pioneer Prototype Unused, 14 Stage, Semi-Auto, Rack & Barrel Plating Plant
An Unused, 14 Stage, Polypropylene Barrel Plating Plant with Transporter. Includes two barrels and can be commissioned and adapted by the OEM.
- Stock No
- PIO5701
- Category
- Electroplating & treatment lines
- Model
- Eagle Engineering and Pioneer Prototype Manual
- Year of Manufacture
- 2023
- Work Envelope (WxDxH mm) [?]
- 830 x 580/1235/1480 x 645
- Process Stages
- 14
- Other Info
- Barrels 2 off 385mm wide 300mm Ø
- Condition
- Brand New, Excellent Condition, Unused, Current Model
- Location
- Hereford, UK
- Direct Site Clearance Price [?]
- £ Login or Register for price.
- Part of a Direct Site Clearance
- Unused Rack & Barrel Semi-Automatic Plating Plant
Balco Engineering Ltd Manual Electropolish Line
An ideal opportunity to acquire a manual Electropolishing Line installed by Balco Engineering Limited in 2013 and subject to an upgrade by them in 2016.The line is utilised in the production of medical implants. The plant is fully operational and can currently be viewed working by prospective buyers.
- Stock No
- TEC300
- Category
- Electroplating & treatment lines
- Model
- Balco Engineering Ltd Manual Electropolish
- Year of Manufacture
- 2013
- Work Envelope (WxDxH mm) [?]
- 200/320/360/390 x 500 x 500
- Process Stages
- 6
- Other Info
- Wall mounted control cabinet containing
- Condition
- From a working environment, Seen working by RSW, Good Condition
- Location
- Sheffield, UK
- Direct Site Clearance Price [?]
- £ Login or Register for price.
- Part of a Direct Site Clearance
- Tecomet Medical Industry Vibratory & Electropolishing Finishing Lines
Balco Engineering Ltd Automatic Electropolish Line
An ideal opportunity to acquire an automatic electropolishing line, installed by Balco Engineering Limited in 2016 utilised in the production of medical implants. The plant is fully operational and can currently be viewed working by prospective buyers.
- Stock No
- TEC400
- Category
- Electroplating & treatment lines
- Model
- Balco Engineering Ltd Automatic Electropolish
- Year of Manufacture
- 2016
- Work Envelope (WxDxH mm) [?]
- 260/360 x 500 x 650
- Process Stages
- 6
- Other Info
- Fume Exhaust System (4,386 CFM)
- Condition
- From a working environment, Seen working by RSW, Good Condition
- Location
- Sheffield, UK
- Direct Site Clearance Price [?]
- £ Login or Register for price.
- Part of a Direct Site Clearance
- Tecomet Medical Industry Vibratory & Electropolishing Finishing Lines
Plasticraft Manganese Phosphate Coating Line
A pre-treatment line in demand for its corrosion-resistant, anti-galling & hardness properties, this manganese phosphate coating line from Plasticraft Ltd is a great opportunity to optimise your steel/steel alloy components for optimum post-paint results.
- Stock No
- ULT750
- Category
- Electroplating & treatment lines
- Model
- Plasticraft Manganese Phosphate Coating Line
- Year of Manufacture
- 2007
- Work Envelope (WxDxH mm) [?]
- 760 x 610 x 900
- Process Stages
- 8
- Other Info
- See full process schedule attached
- Condition
- From a working environment, Seen working by RSW, Good Condition
- Price [?]
- Please call on +44 (0) 1922 45 8000
- Part of a Direct Site Clearance
- Plasticraft Manganese Phosphate Coating Line
Machines & equipment for sale
- Surface Treatment
- Cleaning & Degreasing
- Polishing & Belt Linishing
- Mass Finishing
- Ovens & Furnaces
- Process Cooling
- Shot Blasting
- Dust & Fume Extraction
- Air Compressors
- Rectifiers & Transformers
- Miscellaneous
- Latest Stock
- Special Offers
- Direct From Site Clearances
- Auctions
- Brand New Machines
- Available Immediately
- Sell Your Machine
Machine Alert
Get the latest machines emailed directly to you as they become available to buy online. Sign Up Now