Machinery for the Three Stages of Powder Coating
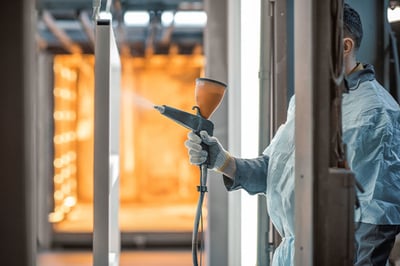
A leading method for high production surface finishing, powder coating is a refined method best known for utilising electrostatic charges to coat components.
However, applying powder is only one part of three stages of production:
- Pre-treatment
- Application
- Curing
Pre-Treatment - Industrial Component Cleaning
For a clean final finish, the component needs to be thoroughly clean of all dust, oils and debris before it can proceed to be powder coated. This can also include inorganic contaminants like rust, mill scale and laser oxide that are side effects of production or parts being refurbished.
The equipment to carry out this process can include wash stations, blast rooms, and dry-off ovens.
Aqueous wash stations such as dip tanks or spray washers would agitate the components in hot water, steam, detergent, and other cleaning solutions to remove the contaminants like grease and oils. This might need to be followed by a dry-off oven to dry the components without leaving any water residue marks.
Solvent cleaners use a different technique to clean parts without using water. Both approaches have their pros and cons but are effective in the right circumstance.
For components that need more TLC than a clean, blast rooms and other shot blasting machinery can be used to refine the profile of the component of rust and scale. Powered by compressed air, small media is shot at the surface to refine the surface of the irregularities. If blasting media is combined with water in a Wet Blast Cabinet the part can be cleaned at the same time as blasting.
Application - Powder Coating Guns
The most widely used method for applying powder to components is Electrostatic Deposition (ESD), featuring an electrostatic spray gun to easily apply the powder coating. The gun is connected to a powder feeder, shooting the powder via an electrostatically charged nozzle. Depending on the gun, this charge can be applied by passing through an ionized electrostatic field in the nozzle or positively charging the particles by rubbing and causing friction against an insulator/conductor inside the gun.
The result of charging the particles causes the stream of powder cloud to adhere evenly to the surface of the component.
With the potential to be a messy process, this would take part in a spray booth to contain the powder, complete with its own extraction system. The extraction system benefits the operator for multiple reasons, including operator safety & comfort.
Another benefit of a Powder Coating Booth fitted with cartridge filters is that it can reduce waste and save on costs for powder. The powder that is unsuccessful in attaching to the component (also known as the overspray) is gathered by the filters during the extraction. These filters are typically located above a recovery bin/hopper, and pulse to release the powder into the bin. This allows the operator to gather and reuse the overspray, also long as they are applying the same finish.
Another popular option for application is fluidized bed powder coating, where the components are dipped in a fluidized bed of powder material. If the bed is pre-heated this allows the component to start curing the powder coating immediately upon application.
Paint Curing - Powder Coating Ovens
For electrostatic deposition applied components that are yet to be cured, the charge of the powder is the only reason the coating stays in place, but once it loses charge it will fall off. Therefore, the curing process is critical to give the coating the durability the finish is known for.
Using an oven made for this process, powder coating ovens are large ovens that heat the air for an even temperature throughout the internal chamber.
The oven would be heated to around 200°C and the component would be placed inside for 10 to 60 minutes. The temperature and duration depends on the size of the component and the specification of the powder.
The result achieved from curing is to melt the powder coating so it bonds together to create a solid and durable film layer over the component.
Do You Have All The Powder Coating Equipment You Need?
As a simple process only made up of 3 stages of easily available and affordable machinery. It’s no wonder powder coating is so popular in the manufacturing industry.
As trusted suppliers of the new and used machinery for each stage of the process, we have been supplying plant & machinery to full production lines in the powder coating industry for years.
If you have an enquiry about our powder finishing equipment or are looking to upgrade/expand your production line, call us at +44(0)1922 45 8000
Or browse our new and use machine stock at:
- Cleaning and Degreasing Machinery
- Shot Blasting Machinery & Equipment
- Powder Coating Wet Paint Plant
- Industrial Ovens
JLS (Redditch) Ltd 300°C Precipitation Hardening & Ageing Oven - AMS2750D
JLS precipitation hardening & ageing, forced convection oven built to AMS2750D & Nadcap class 2 (± 5°C) standard, previously used for the heat treatment of aluminium aerospace components and last calibrated November 2024.
- Stock No
- AEF300
- Category
- Industrial Ovens
- Model
- JLS (Redditch) Ltd Precipitation Hardening & Ageing Oven
- Year of Manufacture
- 2008
- Internal Size (WxDxH mm) [?]
- 1200 x 2500 x 1200
- Max Temp
- 300°C
- Other Info
- Calibrated November 2024 ± 5°C @ 200°C
- Condition
- Seen working by RSW, Excellent Condition
- Location
- Bolton, Greater Manchester, UK
- Price [?]
- Please call on +44 (0) 1922 45 8000
- Part of a Direct Site Clearance
- Aeroforma - Aerospace Quality Machinery
Spray Coating Booth
Powder coating booth with hanging rail, internal light and outlet ducting for connection to suitable dust extraction unit.
- Stock No
- GD866
- Category
- Powder coating, wet paint plant & equipment
- Model
- 1.5M³
- Year of Manufacture
- Unkown
- Work Envelope (WxDxH mm) [?]
- 1000mm x 1000mm x 1500mm
- Process Stages
- Single Stage
- Other Info
- Optional Extraction Point to LH Wall
- Condition
- From a working environment, Good Condition
- Sold As Seen Price [?]
- £ Login or Register for price.
Romer ProfiSpray V Powder Coating Gun
The Romer ProfiSpray V powder coating gun is a high quality powder coating corona gun designed for simple operation with excellent coverage. Programmable control is via a touch screen.
- Stock No
- GD867
- Category
- Powder coating, wet paint plant & equipment
- Model
- Romer ProfiSpray V
- Year of Manufacture
- 2024
- Work Envelope (WxDxH mm) [?]
- N/A
- Process Stages
- Single Stage
- Other Info
- Three Automatic Spray Programs
- Condition
- Brand New, Unused, Current Model
- Availability
- Available for immediate collection
- Price [?]
- £ Login or Register for price.
Gema Auto Reciprocating Roll-On/Roll-Off Powder Coating Booth
Gema reciprocating powder coating plant comprises a booth, reciprocator, guns, powder pump, hopper, control units and systems. Also includes landmarks burners (x2), fire detection, overhead track system and Unicoil boiler suitable for building your own paint line.
- Stock No
- GD869J
- Category
- Powder coating, wet paint plant & equipment
- Model
- Gema ZA06
- Year of Manufacture
- 2013
- Other Info
- Use to build your own Paint line
- Condition
- From a working environment, Seen working by RSW, Excellent Condition, Current Model
- Availability
- Available for immediate collection
- Refurbished Price [?]
- £ Login or Register for price.
- Sold As Seen Price [?]
- £ Login or Register for price.
ERG Process Plant Ltd Ardrox Penetration Application Equipment and Spray Booth with Extraction
This booth can be used for the application of fluorescent dye penetrant and the subsequent penetrant drain and contact time. When the penetrant contact time has expired, parts that have been processed using water washable penetrant are post washed in this booth. In the case of post emulsifiable penetrant, it will be the pre wash.
- Stock No
- GD876J
- Category
- Powder coating, wet paint plant & equipment
- Model
- ERG Process Plant Ltd Ardrox Penetrant Application / Spray Booth
- Work Envelope (WxDxH mm) [?]
- 2000 x 2000 x 2050mm Approx.
- Process Stages
- Ardrox None Destructive Testing (NDT)
- Other Info
- Twin Penetrant Pressure Pot Controls
- Condition
- From a working environment, Good Condition, Current Model
- Sold As Seen Price [?]
- £ Login or Register for price.
ERG Process Plant Ltd Ardrox Penetration Application Equipment and Spray Booth with Extraction
This booth can be used for the application of fluorescent dye penetrant and the subsequent penetrant drain and contact time. When the penetrant contact time has expired, parts that have been processed using water washable penetrant are post washed in this booth. In the case of post emulsifiable penetrant, it will be the pre wash.
- Stock No
- GD877J
- Category
- Powder coating, wet paint plant & equipment
- Model
- ERG Process Plant Ltd Ardrox Penetrant Application / Spray Booth
- Work Envelope (WxDxH mm) [?]
- 2000 x 2000 x 2050mm Approx.
- Process Stages
- Ardrox None Destructive Testing (NDT)
- Other Info
- Penetrant Pressure Pot Controls
- Condition
- From a working environment, Good Condition, Current Model
- Sold As Seen Price [?]
- £ Login or Register for price.
P&P Products QC1200 Quadrant Coater
A P&P Products QC1200 coating machine has been specifically designed to both supersede and complement presently established methods of dip-spin or centrifuge and tumble or barrel coating methods.
- Stock No
- GD881
- Category
- Powder coating, wet paint plant & equipment
- Model
- P&P Products QC1200
- Work Envelope (WxDxH mm) [?]
- 1220mm belt length
- Process Stages
- Spray and Bake
- Other Info
- Belt width 1220mm
- Condition
- From a working environment, Good Condition, Current Model
Finishing Design Services Dip Spin Coating Machine
The dip-spin coating process is one of the simplest and easiest application methods. By placing the parts in the wire mesh basket and loading into the machine. The parts are then submerged into the coating solution and spun to remove any excess as part of a simple automated process.
- Stock No
- GD882
- Category
- Powder coating, wet paint plant & equipment
- Model
- Finishing Design Services Dip Spin
- Work Envelope (WxDxH mm) [?]
- Baskets Ø300mm, 200 and 250mm Tall
- Process Stages
- Dip Spin Automated Cycle
- Other Info
- Siemens TD 200 Controller
- Condition
- From a working environment, Good Condition, Current Model
Romer ProfiSpray V Powder Coating Gun
The Romer ProfiSpray V powder coating gun is a high quality powder coating corona gun designed for simple operation with excellent coverage. Programmable control is via a touch screen.
- Stock No
- GD883
- Category
- Powder coating, wet paint plant & equipment
- Model
- Romer ProfiSpray V
- Year of Manufacture
- 2024
- Work Envelope (WxDxH mm) [?]
- N/A
- Process Stages
- Single Stage
- Other Info
- Three Automatic Spray Programs
- Condition
- Brand New, Unused, Current Model
- Availability:
- In stock now
- Price [?]
- £ Login or Register for price.
Romer ProfiSpray V Powder Coating Gun
The Romer ProfiSpray V powder coating gun is a high quality powder coating corona gun designed for simple operation with excellent coverage. Programmable control is via a touch screen.
- Stock No
- GD884
- Category
- Powder coating, wet paint plant & equipment
- Model
- Romer ProfiSpray V
- Year of Manufacture
- 2024
- Work Envelope (WxDxH mm) [?]
- N/A
- Process Stages
- Single Stage
- Other Info
- Three Automatic Spray Programs
- Condition
- Brand New, Unused, Current Model
- Availability:
- In stock now
- Price [?]
- £ Login or Register for price.
SNOL 350°C Industrial Oven Range
350°C general purpose batch ovens, ideal for a vast range of low temperature thermal processes such as drying, curing and pre-heating.
- Stock No
- NEW070
- Category
- Industrial Ovens
- Model
- SNOL
- Internal Size (WxDxH mm) [?]
- Various
- Max Temp
- 350°C
- Condition
- Brand New
- Availability:
- Available subject to build time
- Price [?]
- Please call on +44 (0) 1922 45 8000
SNOL 650°C High Temperature Oven Range
General purpose high temperature, industrial, batch ovens which set the standard for a wide range of industrial processing applications
- Stock No
- NEW071
- Category
- Industrial Ovens
- Model
- SNOL
- Internal Size (WxDxH mm) [?]
- Various
- Max Temp
- 650°C
- Condition
- Brand New
- Availability:
- Available subject to build time
- Price [?]
- Please call on +44 (0) 1922 45 8000
SNOL 650°C High Temperature Oven with Powered Door
General purpose high temperature, industrial, batch oven suitable for a wide range of industrial processing applications. Includes a vertical powered door.
- Stock No
- NEW072
- Category
- Industrial Ovens
- Model
- SNOL
- Internal Size (WxDxH mm) [?]
- 600 x 750 x 900
- Max Temp
- 650°C
- Availability:
- Available subject to build time
- Price [?]
- Please call on +44 (0) 1922 45 8000
SNOL Custom Build Furnaces & Ovens
Custom built ovens and furnaces to meet your project requirements and standards.
- Stock No
- NEW079
- Category
- Industrial Ovens
- Model
- SNOL
- Condition
- Brand New
- Availability:
- Available subject to build time
- Price [?]
- Please call on +44 (0) 1922 45 8000
Romer 200°C Industrial Oven Range
200°C general purpose, electric, batch ovens from 3.4m3 upwards. Ideal for a vast range of low temperature thermal processes such as drying, curing and pre-heating.
- Stock No
- NEW080
- Category
- Industrial Ovens
- Model
- Romer
- Internal Size (WxDxH mm) [?]
- Various
- Max Temp
- 200°C
- Other Info
- Touchscreen Control plus iCure Software
- Condition
- Brand New
- Availability:
- Available subject to build time
- Price [?]
- Please call on +44 (0) 1922 45 8000
Machines & equipment for sale
- Surface Treatment
- Cleaning & Degreasing
- Polishing & Belt Linishing
- Mass Finishing
- Ovens & Furnaces
- Process Cooling
- Shot Blasting
- Dust & Fume Extraction
- Air Compressors
- Rectifiers & Transformers
- Miscellaneous
- Latest Stock
- Special Offers
- Direct From Site Clearances
- Auctions
- Brand New Machines
- Available Immediately
- Sell Your Machine
Machine Alert
Get the latest machines emailed directly to you as they become available to buy online. Sign Up Now